Z House
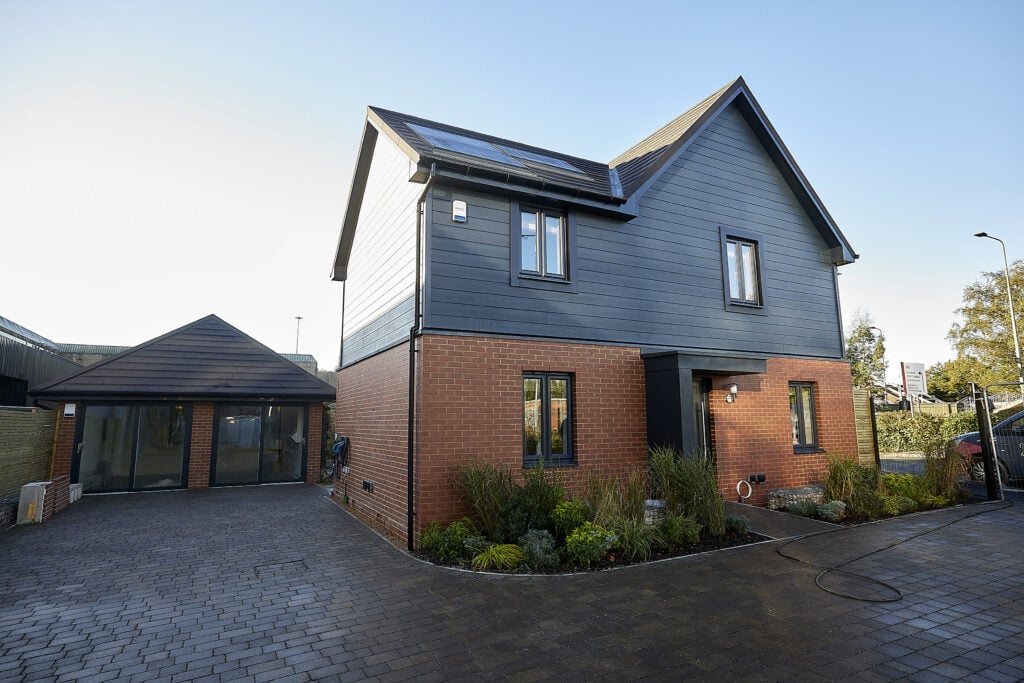
Key Sustainability Objectives/ Outcomes
Zero Carbon: Achieve 100% regulated energy – achieved 125% regulated and unregulated energy.
Low Embodied Carbon: Challenged supply chain to reduced thicknesses of products and use more recycled/sustainable materials.
Smart:To be intelligent enough to use and distribute power – achieved through Tribe’s smart energy management system together with agile tariffs supplied through Octopus.
Biodiversity: Demonstrate a positive ecological impact through supporting biodiversity and wildlife – RSPB Gold Standard Award for the garden landscaping.
Water: Internal water use to be 90 litres per person per day – smart water systems used to achieve this (atomising shower, motion detectors).
Health and wellbeing: Use products that deliver healthier environments – plaster and paints help absorb pollutants (VOCs) and eliminate viruses: air quality improved.
Skills: Support reducing the reliance for on-site skills – advanced MMC, precast concrete floors, offsite panelised masonry systems and closed panel timber frame with factory fitted windows and cladding.
Notable Approaches And Solutions
Through Barratt’s partnership with Bison Forterra, they developed an off-site manufactured, panelised masonry system (Quickwall). The innovative product is an example of a solution to address the industry wide dual challenge of the shortage of skilled bricklayers and an aging workforce in the UK.
The system connects to the timber frame using brackets and is crane lifted into position, reducing the need for scaffolding on-site (which can add H&S risks and cost to a project). The product also ensures greater quality therefore reducing site waste, and increasing the speed of builds from c.24 weeks to c.12-14.
The tiles in the kitchen and bathroom were designed to be 20% slimmer with a depth of (8mm rather than the standard 10mm) which then reduced carbon emissions both in the manufacturing and the transportation of the product to site; thus reducing the overall embodied carbon of the product.
Lessons Learnt
The original Alderney housetype, which the Z House was based on, had to be adapted to accommodate the cylinder needed for the air source heat pump (ASHP), which in turn increased the overall area of the house.
In response to the Heat and Building Strategy, it is likely that gas boilers will be phased out in favour of low carbon heating systems such as ASHPs. With the use of an ASHP, larger radiators had to be accounted for so Barratt would need to consider whether this is a viable solution moving forward (do customers want larger radiators?) or the alternative is to look into other heating solutions which would work better with ASHPs.
Due to the sheer number and variety of different technologies in the house, the integration and communication between them was challenging; in particular getting the heating systems to work together. In order for the coherent, smart heating system to work as intended, technicians from each of the individual heating systems were brought in to share their expertise and communicate with one another on how each of their systems operated, and then had to work together to find the best solution.
Main partners:
- University of Salford – Lead Partner
- AIMCH – Funding and Dissemination
- Oregon – Timber Frame Supplier
- Optima Offsite – Lead Project/Design Manager
- Bison Precast – Supplier of Precast Concrete Systems
- Forterra – Supplier of Panelised Masonry Systems
- GTC/Metropolitan – MEP Design
- Eco2Solar – PV Suppliers
- Clarkson Evans – Electrical Contractor
- Octopus Energy – Green Energy Supplier
Supporting partners: AEG, AICO, Airlite, Aqualisa, ARC, British Gypsum, BT, Cundall, Darren Evans, DiscreteHeat, Donaldson Timber, Dulux, Electrolux, Envirovent, Eurocell, Geberit, Glidevale, Google, Golby + Luck, Hedera Screens, Ian Firth, InfraRedReplacingGas, IOBAC, James Hardie, Johnson Tiles, Kelda Showers, Legrand, Light Source Labs, Marshalls, Metrotile, Mitsubishi, Nissan, Polypipe, Recoup, RSPB, SDS, Sky, Staircraft, StormKing, Symphony, Tenmat, The Irresistible Group, Thermal Economics, Xtratherm.
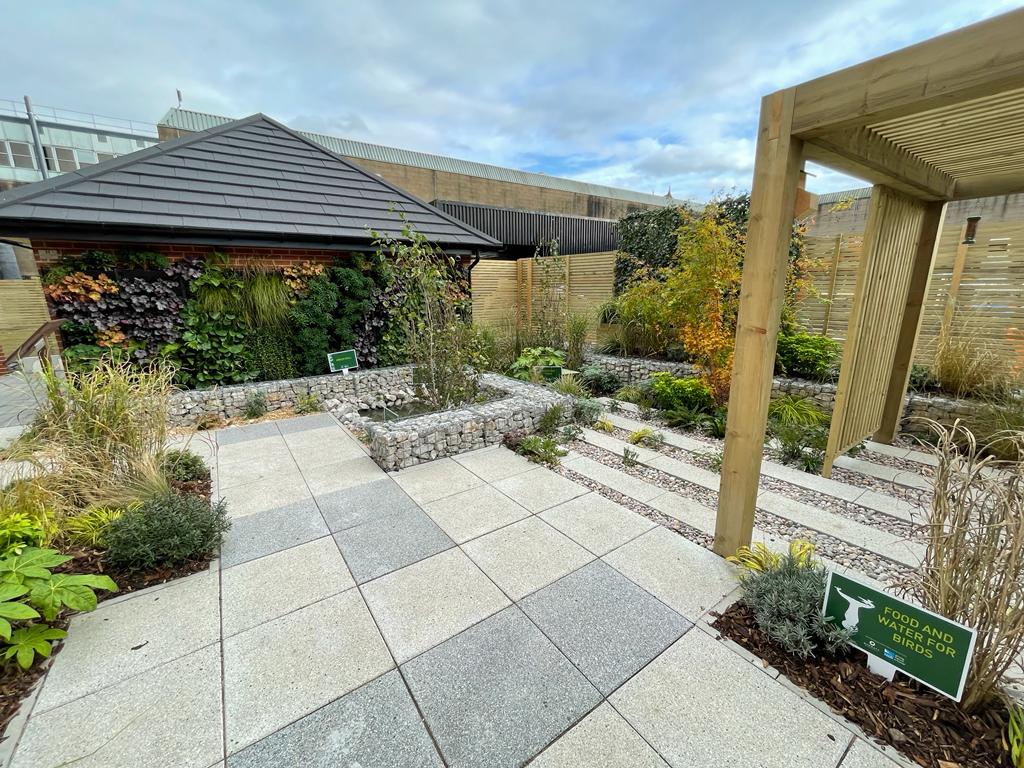
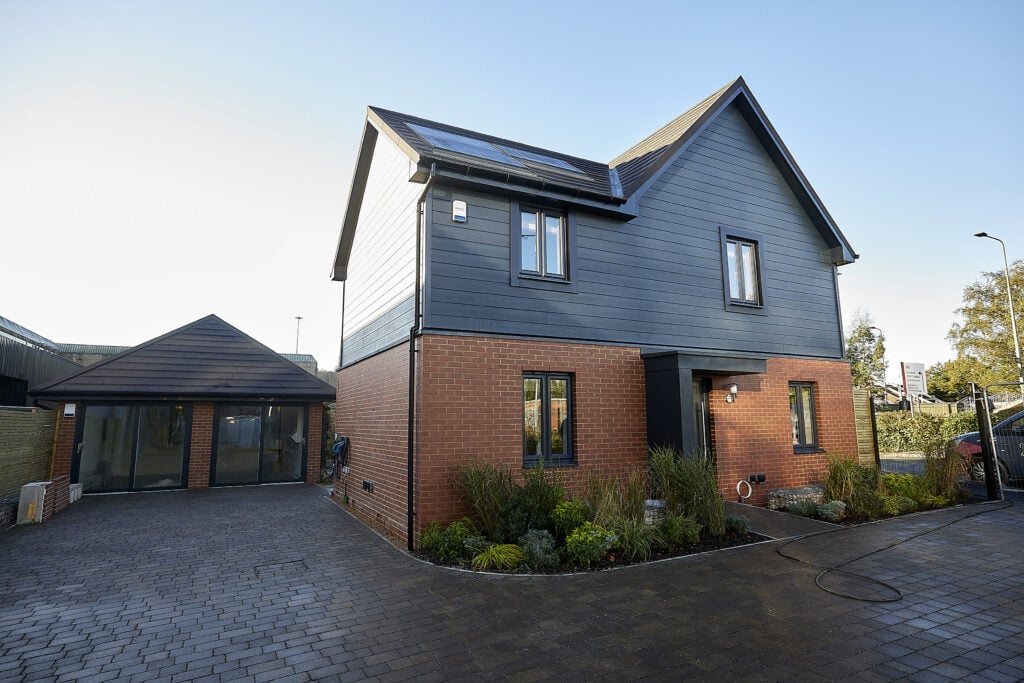
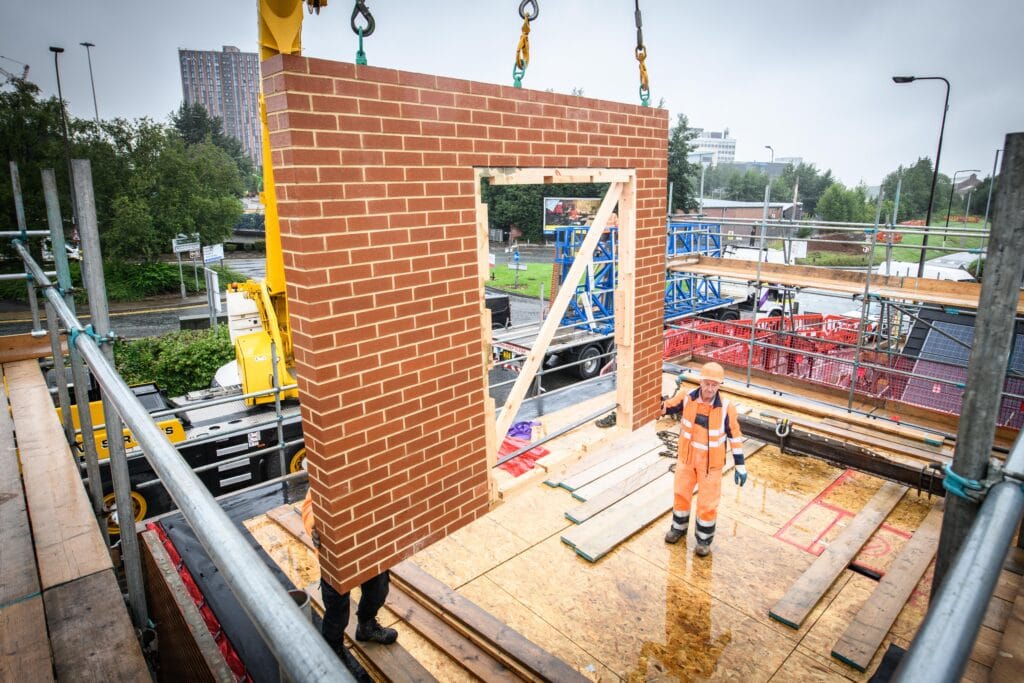
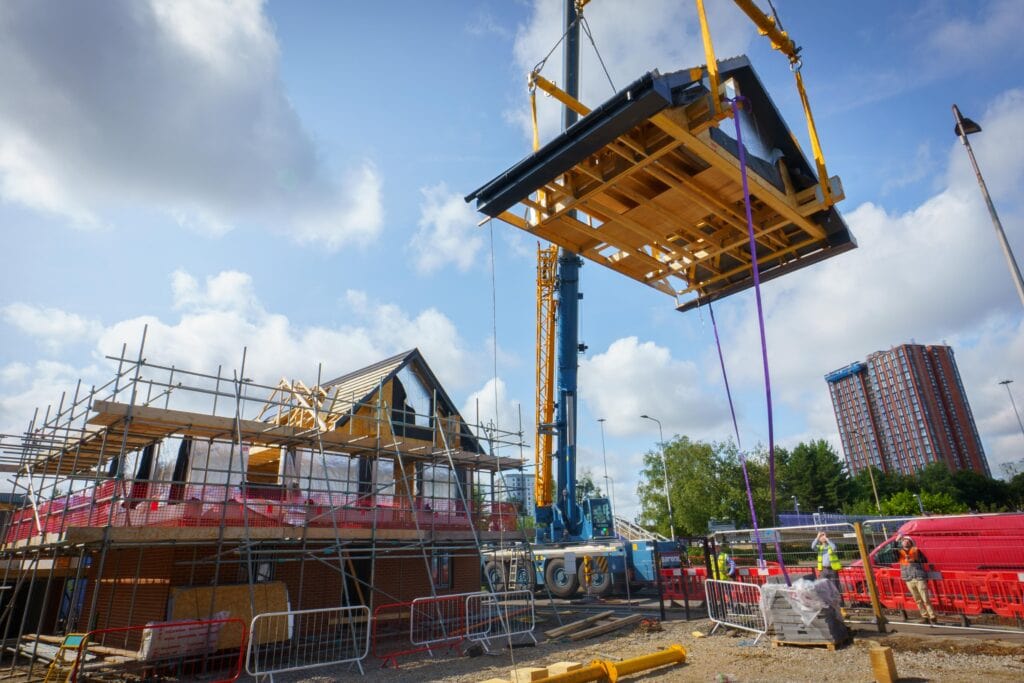
Related members
Related
Active Office and Active Classroom

BEN – The Balanced Energy Network
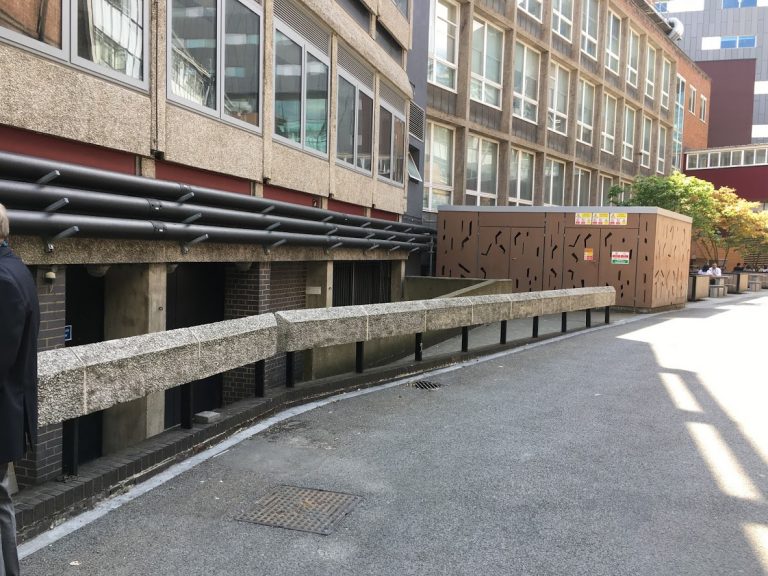
Design for Future Climate – Innovate UK
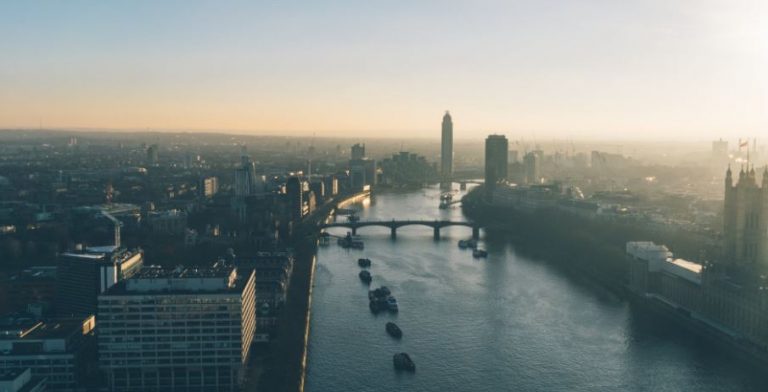
GSK Centre for Sustainable Chemistry
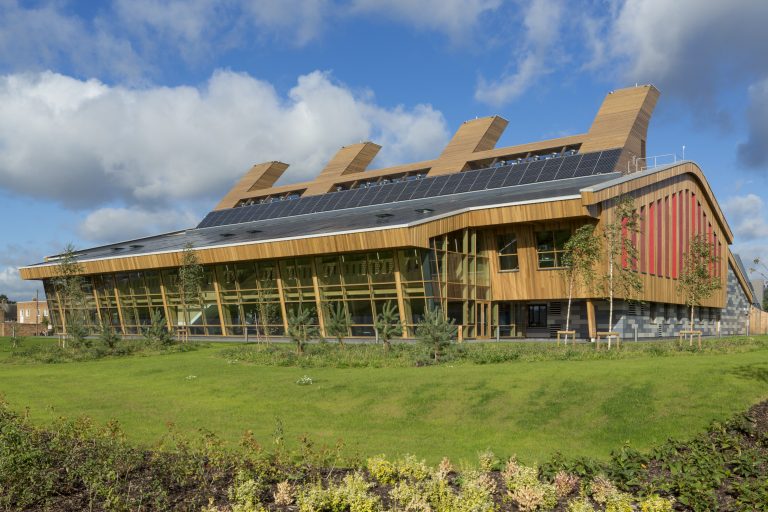