Tempo
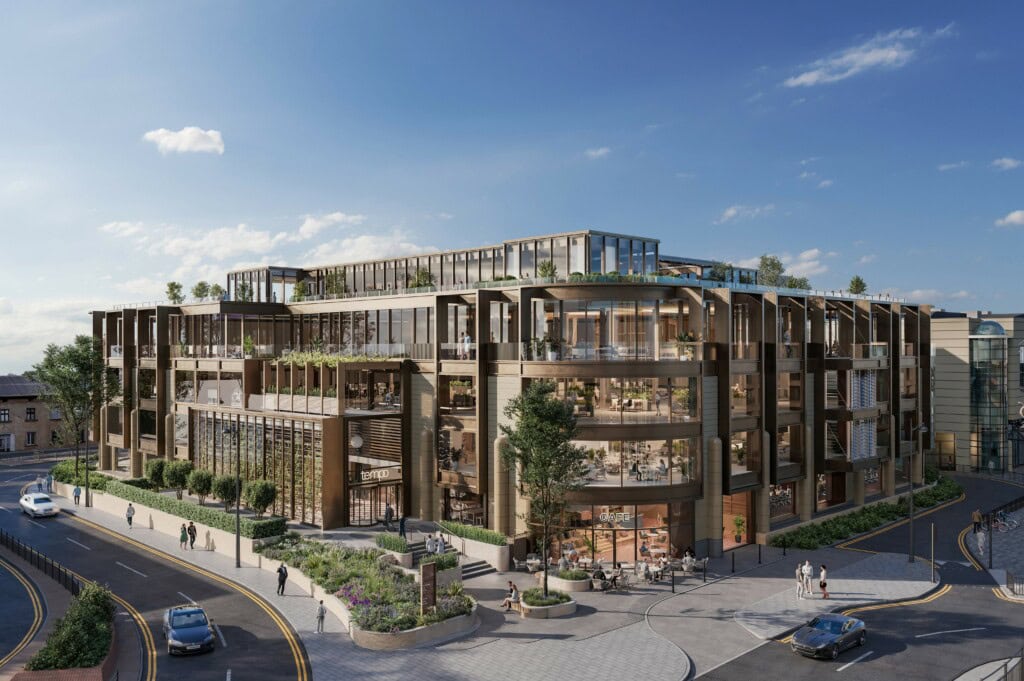
Key Sustainability Objectives/ Outcomes
Climate change mitigation
The carbon assessments achieved the below figures at stage 4 design:
- Upfront Carbon (A1 A5) – 393 kg CO2e/m2,
- Embodied Carbon ( A1-A5, B1–B5, C1-C4) 840 kg CO2e/m2
- Operational Energy – 99.8 kWh/m2 per annum
This was based on most of the structure and façade being retained, with window replacements and the addition of an upper floor. The most impactful measures included; switching from gas boilers to ASHP, improving the efficiency of the AHUs (Air Handling Units), implementing demand-led ventilation, and refining the fabric performance.
As part of the Design for Performance process, it was necessary to model ‘off-axis scenarios’. These are iterations of the energy model that consider potential variations from the baseline design, such as future increased summer temperatures, failure or mis-operation of key systems, changes to occupancy, or increased air permeability.
The modelled operational energy performance of the building – which was completed in line with NABERS Design for Performance standards – was sufficient to achieve a NABERS 5* rating at the design stage, including the necessary margin.
Health, well-being and social value
Targeting £70 – £111million in social value over the lifecycle of the development through:
- Jobs: promoting local skills and employment
- Growth: supporting growth of responsible regional business
- Social: healthier, safer, and more resilient communities
Lessons Learnt
The challenges the Design for Performance (DfP) process:
- Plant efficiencies need to be maximised and pressure drops in ductwork reduced. This requires more space than typical installations.
- Any spaces that may operate out of hours, such as a cafe, should be on independent systems. This avoids operating the main central plant for small loads.
- Refrigerant leakage is a major factor in whole-life carbon. This accounts for 17% of the overall emissions, so using low Global Warming Potential (GWP) refrigerants is key. This was a major factor in why an ASHP solution was progressed as opposed to VRF.
- Enhancing the metering strategy to monitor the energy usage of all MEP services can allow the landlord to investigate and inform the maintenance of any equipment that is using more energy than the intended design.
- Plant efficiencies need to be maximised and pressure drops in ductwork reduced. This requires more space than typical installations.
- Any spaces that may operate out of hours, such as a cafe, should be on independent systems. This avoids operating the main central plant for small loads.
- Refrigerant leakage is a major factor in whole-life carbon. This accounts for 17% of the overall emissions, so using low Global Warming Potential (GWP) refrigerants is key. This was a major factor in why an ASHP solution was progressed as opposed to VRF.
- Enhancing the metering strategy to monitor the energy usage of all MEP services can allow the landlord to investigate and inform the maintenance of any equipment that is using more energy than the intended design.
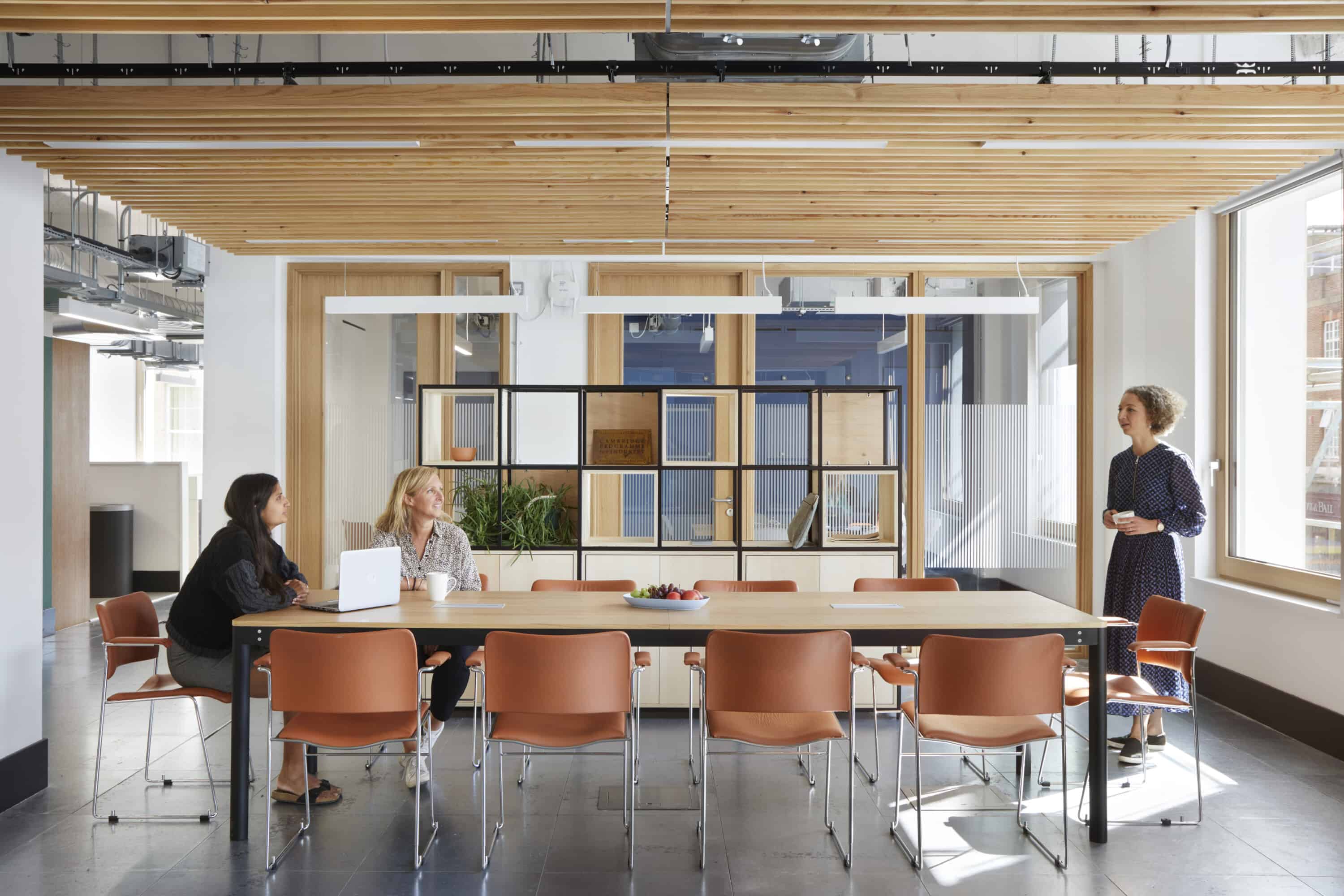
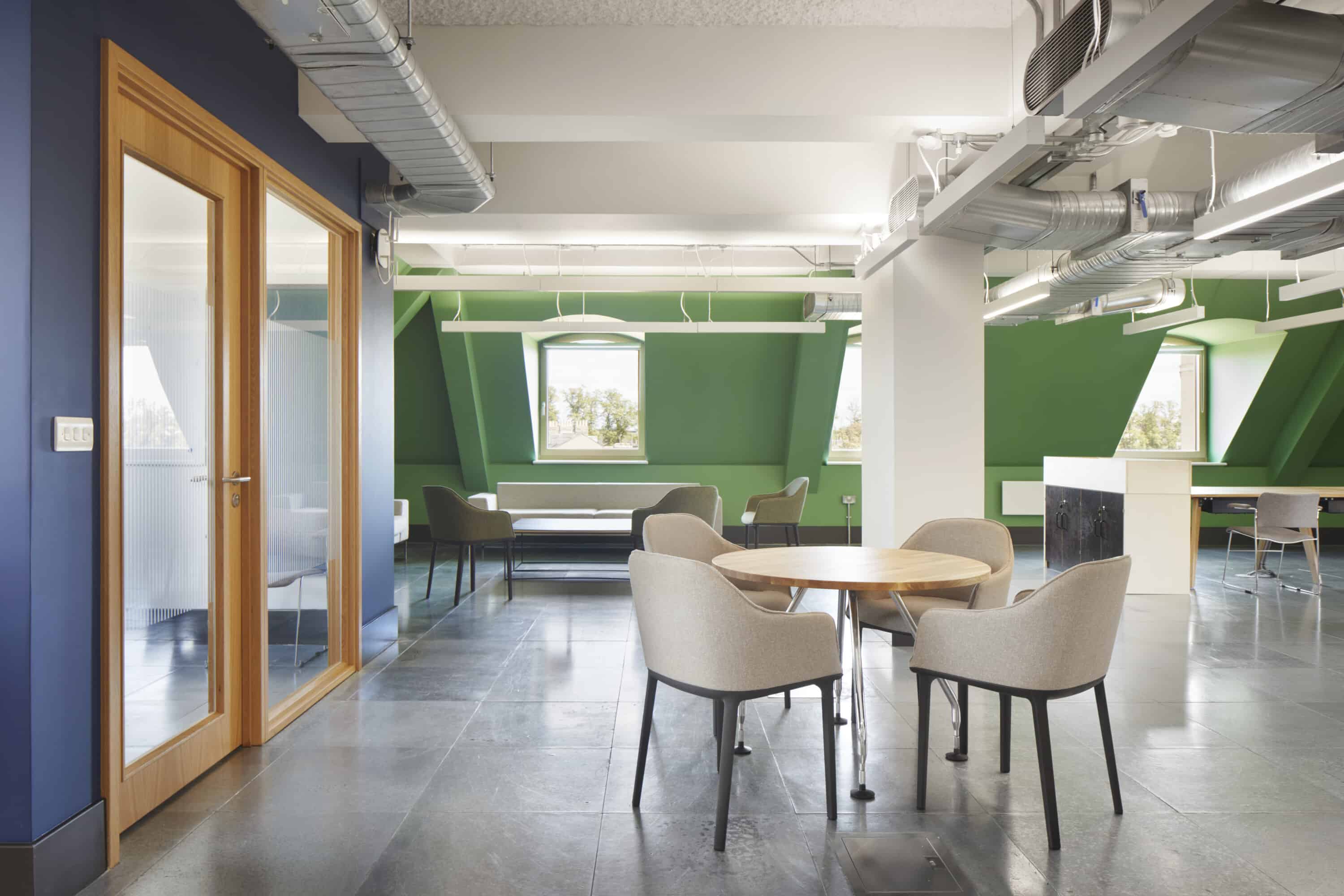
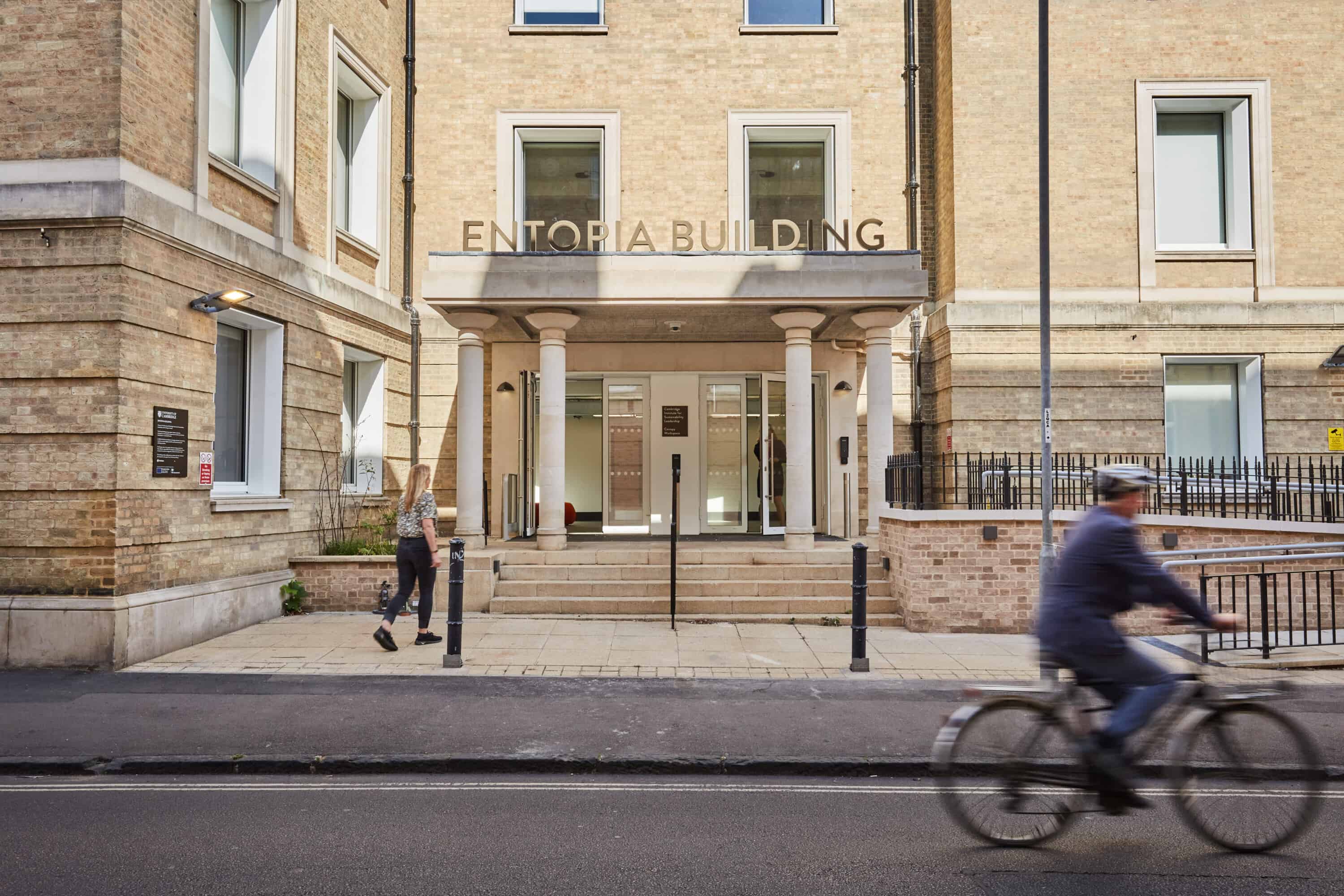
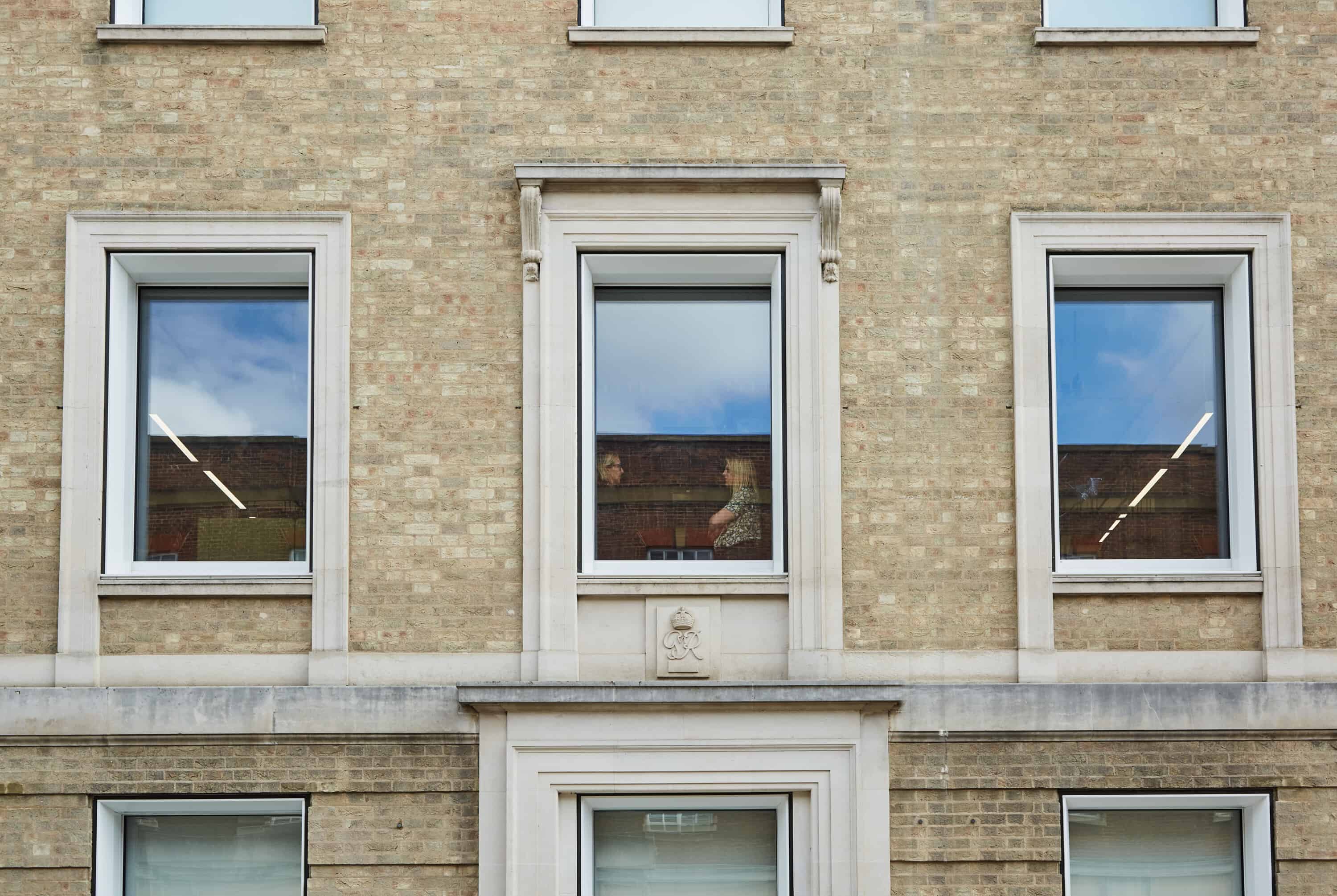
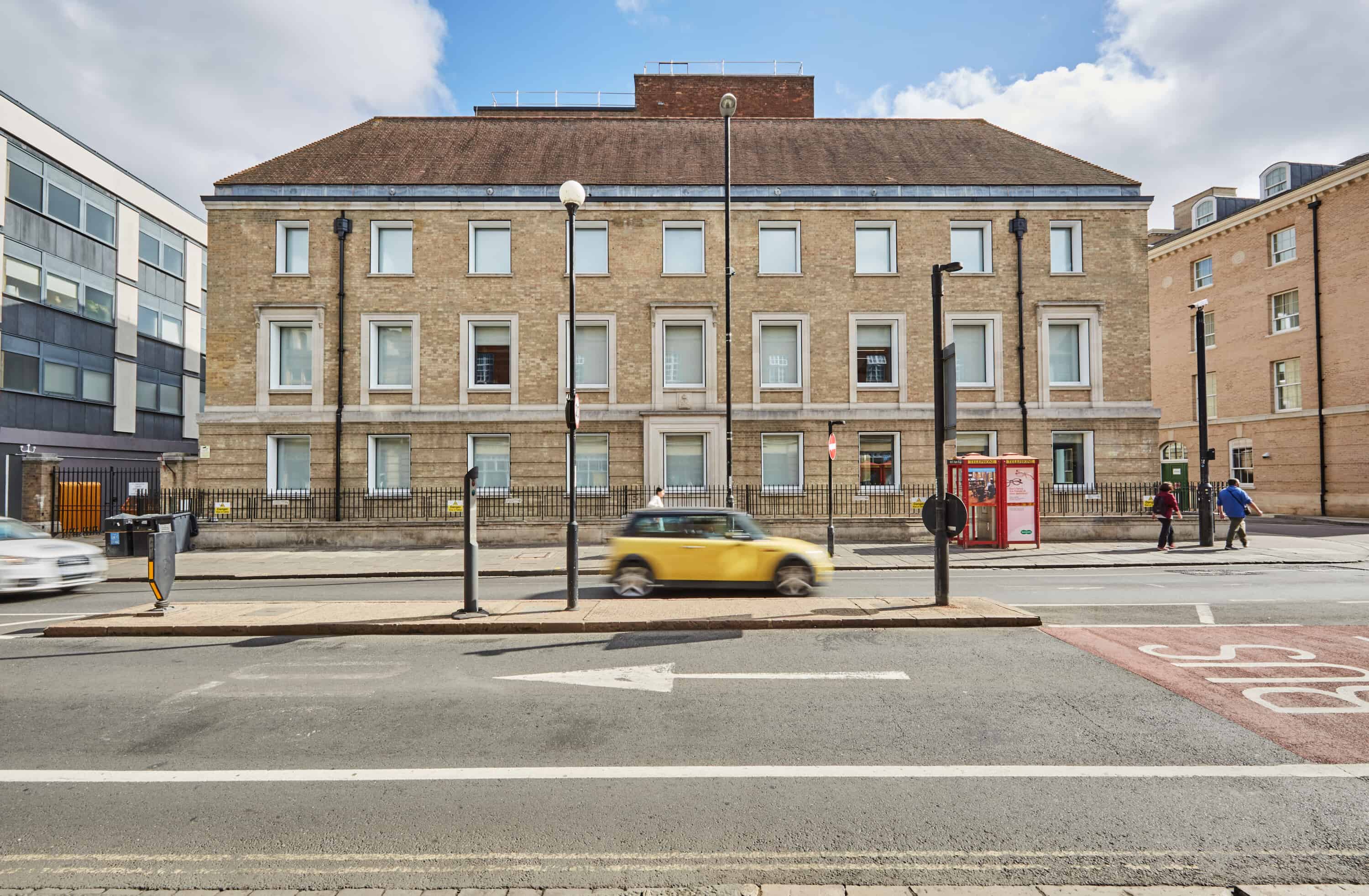
Related members
Related
5 New Street Square
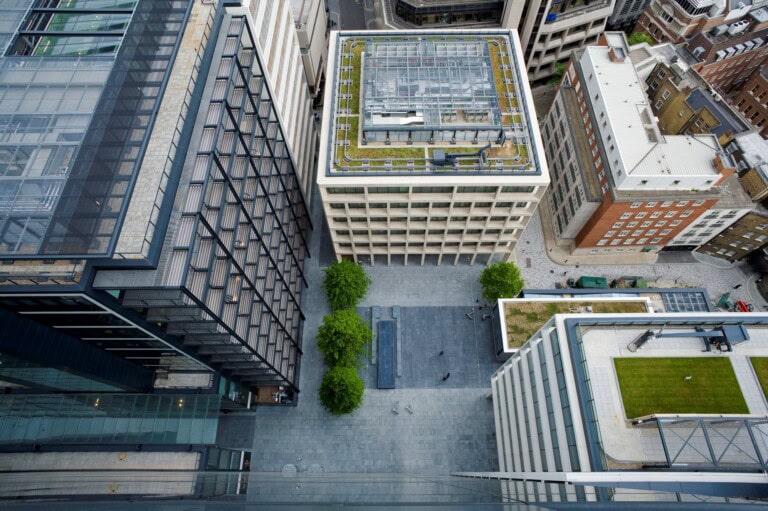
134-138 Edmund Street
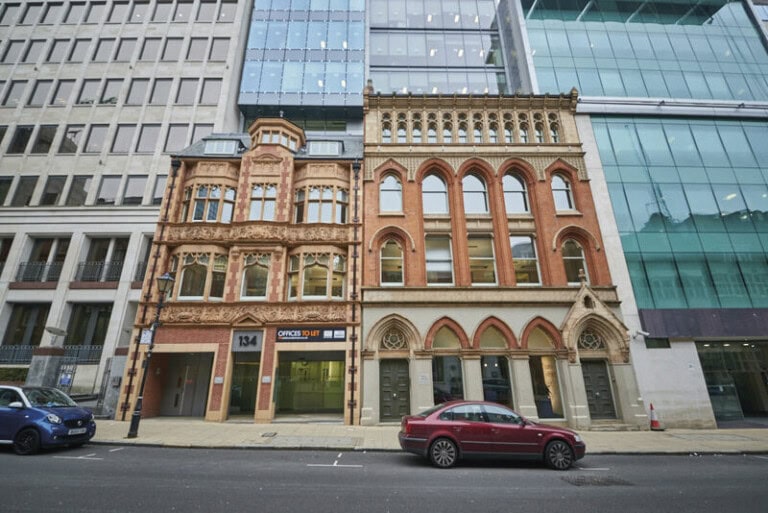
1 & 2 Stephen Street
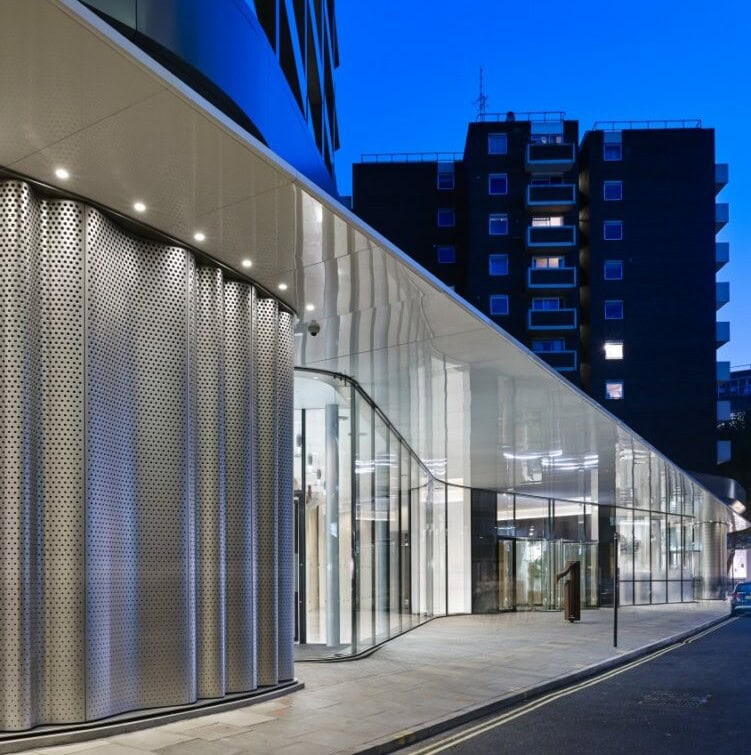
Minerva House
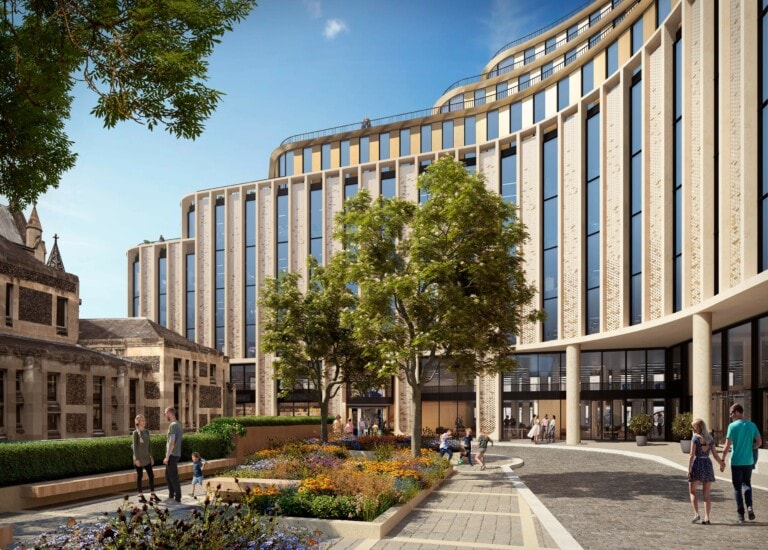