3D printed concrete beams designed to use less material
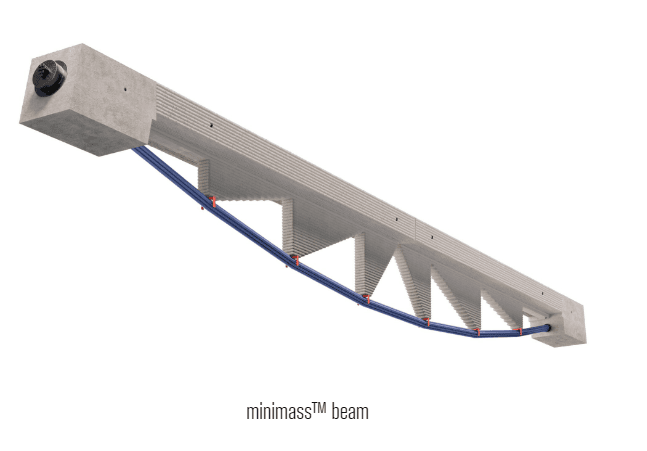
Problem Addressed
The built environment is directly responsible for 25% of UK emissions, lifting to 42% if you include surface transport. In order to reach Net Zero by 2050, the roadmap for the construction industry, from the Global Cement and Concrete Association (GCCA), requires a 25% reduction in emissions by 2030, compared to 2020. Sustainable development in 21st century must include concrete solutions but there is no need to wait until 2030 for meaningful reductions in embodied carbon.
Case Study
There is no built case study available but the product has passed a range of laboratory tests and is now being marketed to projects in UK, Europe and Australia. Furthermore, a series of 6m long physical prototypes have been printed and assembled for destructive load testing. Working with a range of industry leaders, this testing process has been essential to validate minimass for the construction industry.
Facts and Figures
This page presents data, evidence, and solutions that are provided by our partners and members and should therefore not be attributed to UKGBC. While we showcase these solutions for inspiration, to build consensus, and create momentum for climate action, UKGBC does not offer commercial endorsement of individual solutions. If you would like to quote something from this page, or more information, please contact our Communications team at media@ukgbc.org.
Related
Sensors and AI to predict concrete curing time
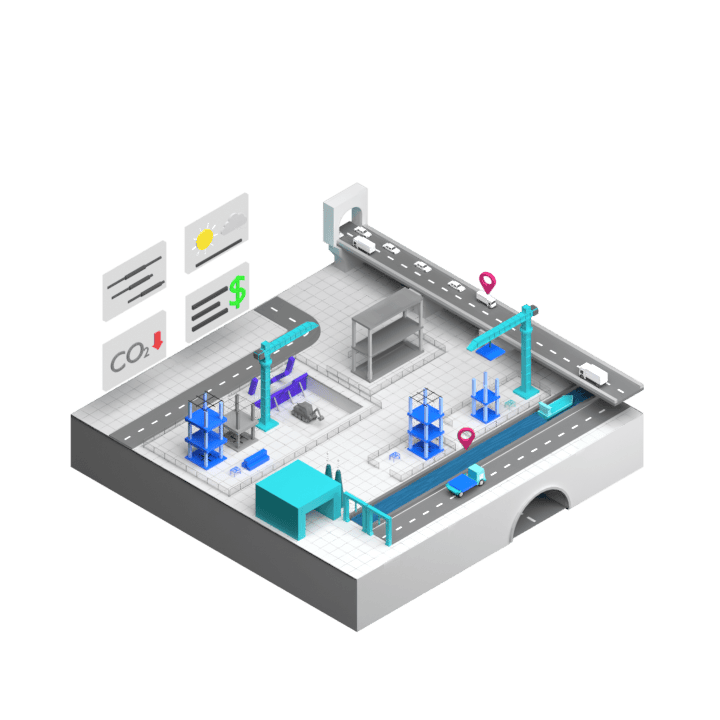
Decarbonising Precast Concrete
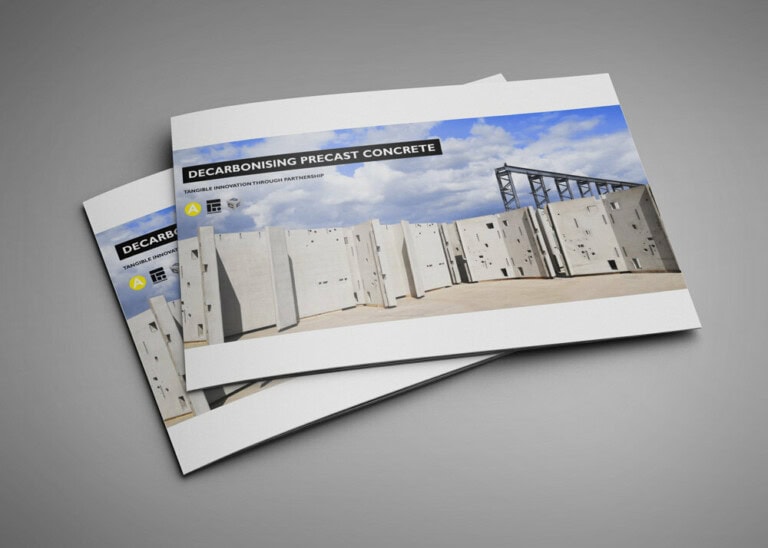
Zero cement concrete
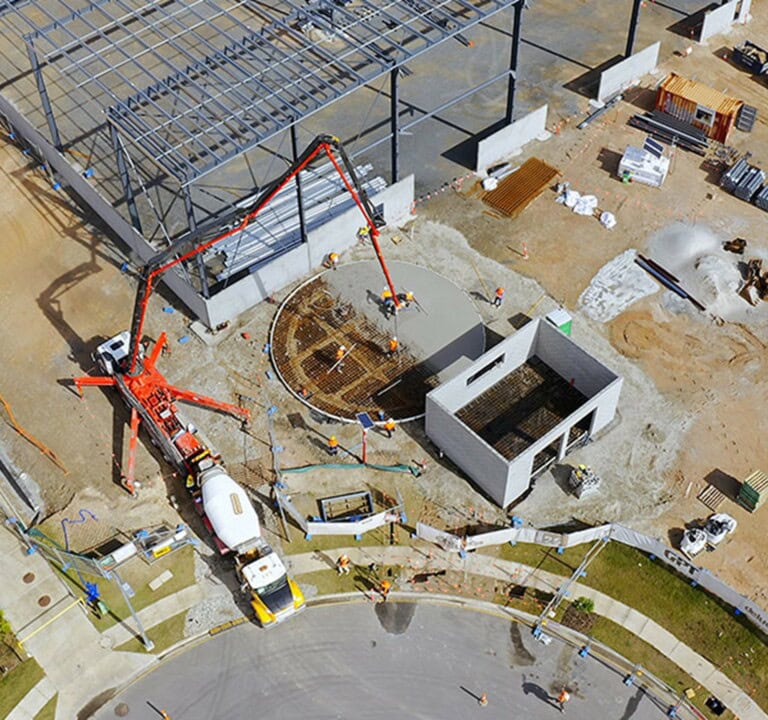
Cement alternatives
