Sensors and AI to predict concrete curing time
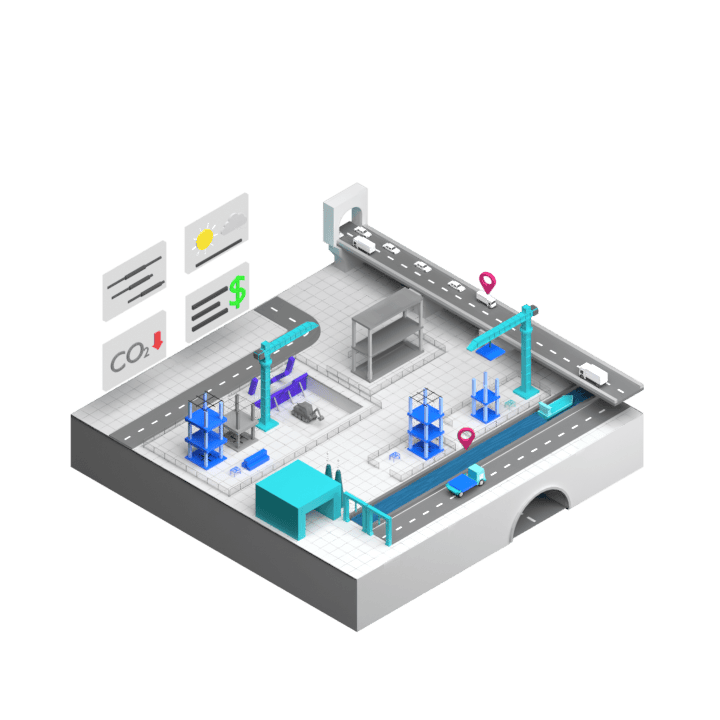
Problem Addressed
Concrete is a construction resource requiring significant decarbonisation in the race to Net-Zero. Contractors often operate in the blind in terms of concrete maturity, due to antiquated testing methods. As such, concrete is often over-performant in order to increase safety margins, resulting in high embodied carbon mixes. Additionally, novel low carbon concrete chemistries are often more complicated to work with and traditional strength testing methodologies make them unfeasible at scale.
Case Study
St Johns Manchester Good Yard
The site
Manchester Goods Yard is the creative and professional hub of the £1bn St John’s quarter development with 30,000m2 of floor space, across nine floors, dedicated to offices, co-working spaces and retail. Careys were subcontracted to Leandlease to construct the frame which featured a PT slab design.
The first and second steel strand tensions were the critical path activities and could only commence once the strength had exceeded 10MPa and 25MPa, respectively. Precise awareness of the concrete strength development was, therefore, critical to the swift progression of each pour cycle.
Tensioning strands is also a high-risk activity that can lead to burst anchors, cracked concrete and, worse, safety issues if performed too early. Therefore, the accuracy of the concrete strength measurements was paramount.
The solution
The Mesh sensors and wireless network were easily set up then, for 11 months and 97 concrete pours, reliably collected and wirelessly transmitted data, every 20 minutes, without fail. The 6-month battery life of the Nodes, rugged design and 50+ meter wireless range meant that managing the system during construction was simple.
Using live strength data and AI-enabled predictions, the project team could plan and execute tensioning and striking ahead of up to 24hrs ahead of schedule for every pour. The accurate, temperature-sensitive calculations meant that Careys could tension and strike slabs all year round, without risking burst anchors due to strength overestimates.
Value delivered
- Saved up to 24hr/pour: scheduling and executing tensioning and striking of every slab pour up to 24hrs sooner than if they had used cubes
- Improved quality and safety: In-situ, temperature-sensitive, strength calculations are accurate regardless of the weather conditions. Year-round, Careys could tension slabs, confident that anchors would not burst; reducing the risk of compromising the quality of the slabs whilst safeguarding those on site. The project was without incident over 30,000m^2 of concrete poured
- Eliminated reliance on site cubes: ConcreteDNA automated concrete testing; reducing the man-hours invested in preparing, curing and crushing cubes. Delays caused by low-cube strengths resulting from poor cube preparation were eliminated and the project team could focus on managing the project rather than chasing cube results.
More Case Studies
https://www.converge.io/case-studies
Facts and Figures
This page presents data, evidence, and solutions that are provided by our partners and members and should therefore not be attributed to UKGBC. While we showcase these solutions for inspiration, to build consensus, and create momentum for climate action, UKGBC does not offer commercial endorsement of individual solutions. If you would like to quote something from this page, or more information, please contact our Communications team at media@ukgbc.org.
Related
Sensors and AI to predict concrete curing time
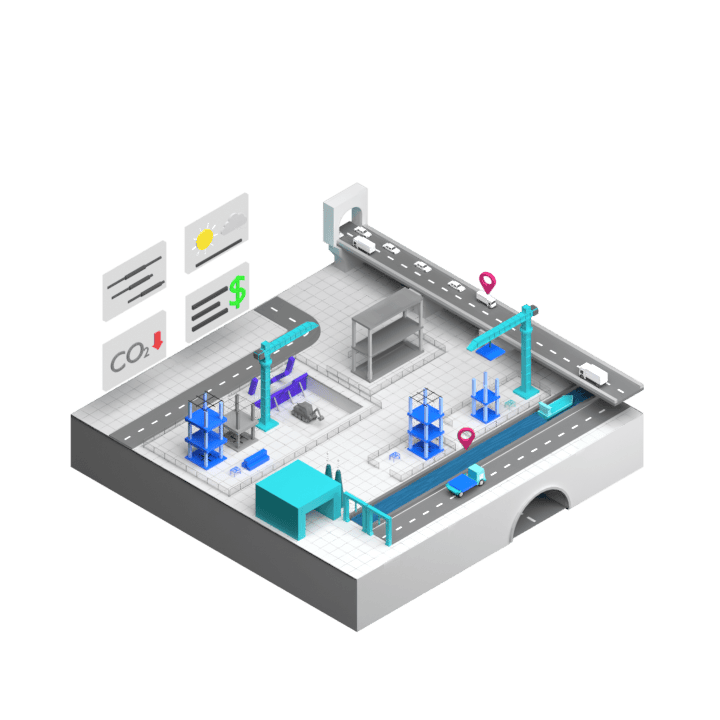
Zero cement concrete
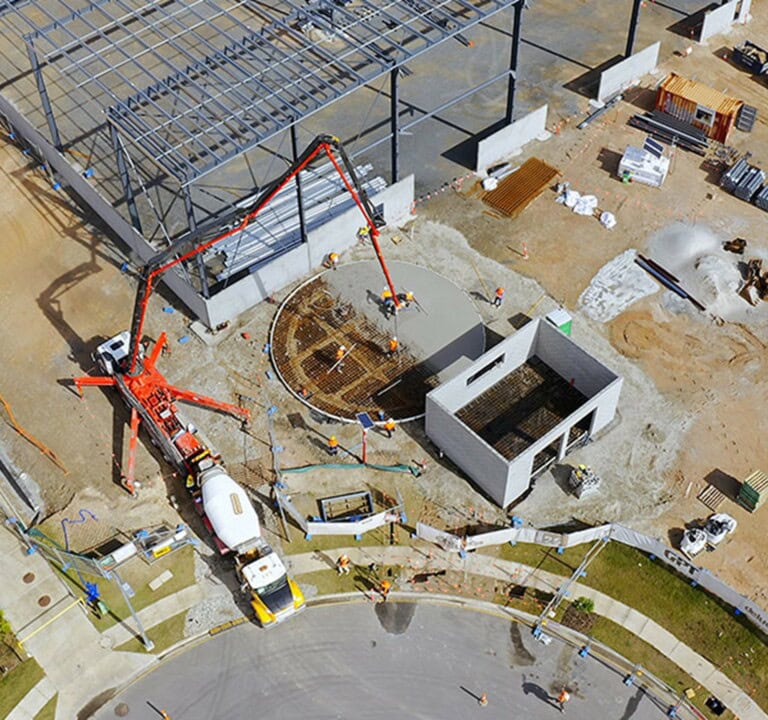
CarbonCure Ready-Mix
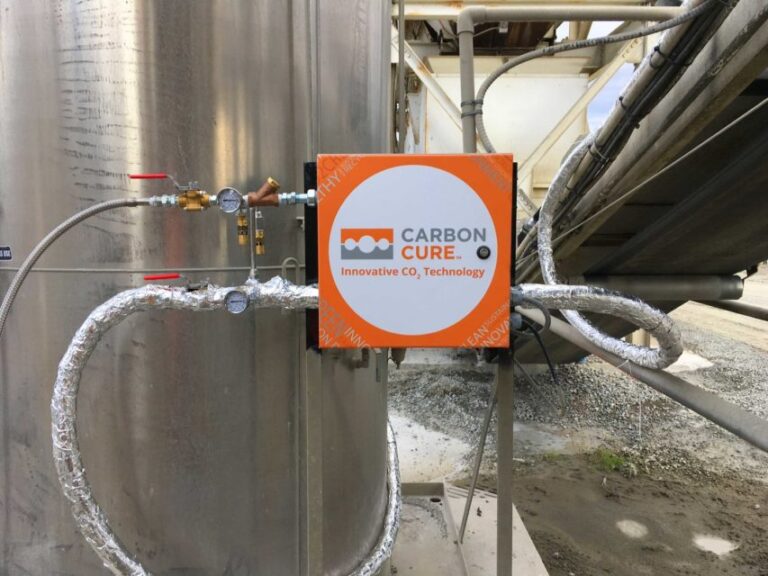
3D printed concrete beams designed to use less material
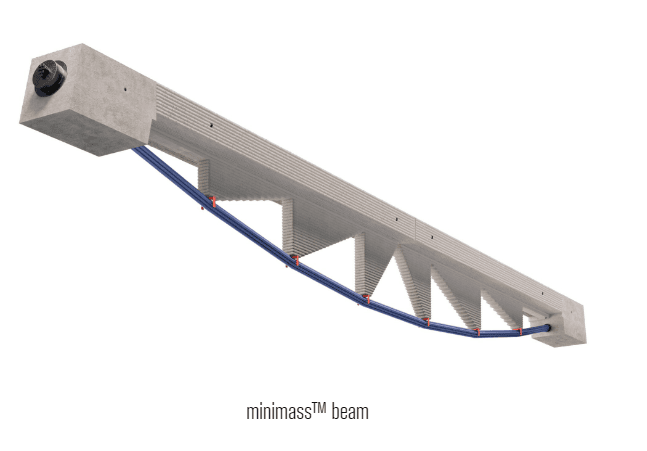