Brunel Building
The Brunel Building in London aims to reduce its carbon footprint using solutions like aquifer thermal systems and incorporating reused materials.
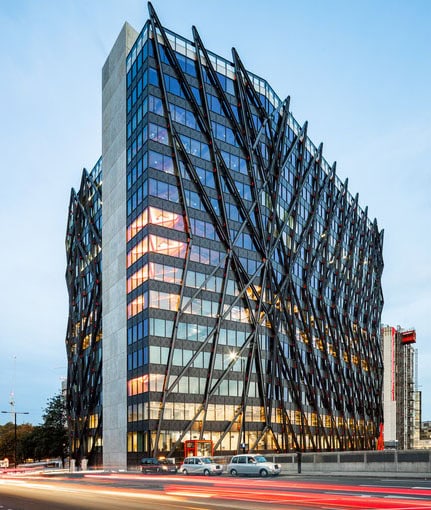
Highlights
-
The building achieved a BREEAM 2014 ‘Excellent’ rating, a Wired ‘Platinum’ rating and a LEED ‘Gold’ rating.
- Operational and embodied carbon assessments were completed during the early stages of the project to identify opportunities for reducing carbon emissions throughout the design process.
- An aquifer thermal energy storage (ATES) system utilising two 180m-deep boreholes provides low carbon heating and cooling to the building, taking advance of the stable ground temperatures.
- Low energy fan coil units can be individually controlled to improve energy consumption and comfort.
- Exposed concrete soffits and thermal mass improve occupancy comfort during heat wave conditions.
- The estimated operational energy consumption could achieve a 71% improvement over the energy benchmark of a typical Econ19 office fit out, and a 54% improvement over a good practice fit out.
- Exposing the structure both internally and externally helped to reduce embodied carbon. Avoiding suspended ceilings saved 540 tCO2e, fly ash replacement in the concrete saved over 1,000 tCO2e and employing self-finishing concrete saved 18 tCO2
- A high-level health and wellbeing review was carried out on the base build to ensure the building was WELL enabled should a tenant wish to achieve the certification for their fitout areas.
- More than 98% of construction waste was recycled.
- Grey water from the showers is recycled and used to flush the WCs which reduces the potable water demand by up to 30%.
- Aluminium used in the façade contained 65% recycled content.
- A sustainable procurement policy was in place during construction which included requirements for: responsibly sourced materials, materials with a high recycled content, regional materials and waste minimisation and recycling.
- By employing Design for Manufacture and Assembly (DfMA), the design team and contractor Laing O’Rourke were able to significantly reduce material waste onsite; more than 98% of construction waste was recycled.
For Further Information…
Please contact: Olivia Allen, Sustainability Manager
Related members
Related
8 Bishopsgate
A 50-storey office tower that uses passive design principles and responsive building systems to optimise reductions in carbon.
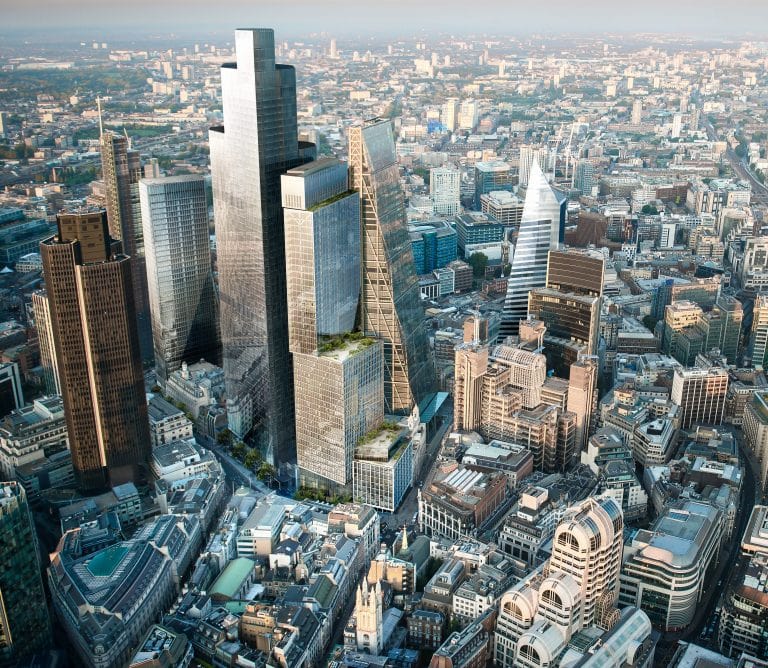
Brunel Building
The Brunel Building in London aims to reduce its carbon footprint using solutions like aquifer thermal systems and incorporating reused materials.
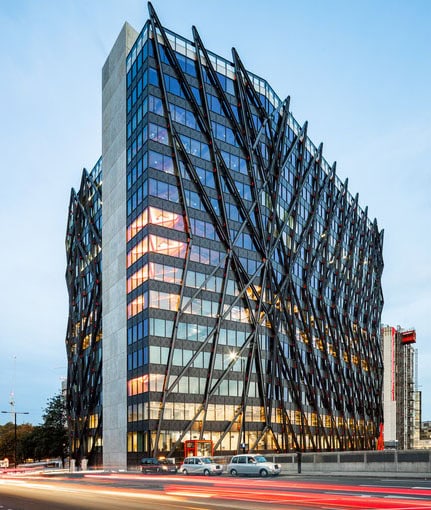
WWF-UK Living Planet Centre
WWF’s UK Headquarters showcase its value for environmental sustainability, achieving a 42% reduction in embodied carbon and net zero carbon in operation by offsetting using the Gold Standard.
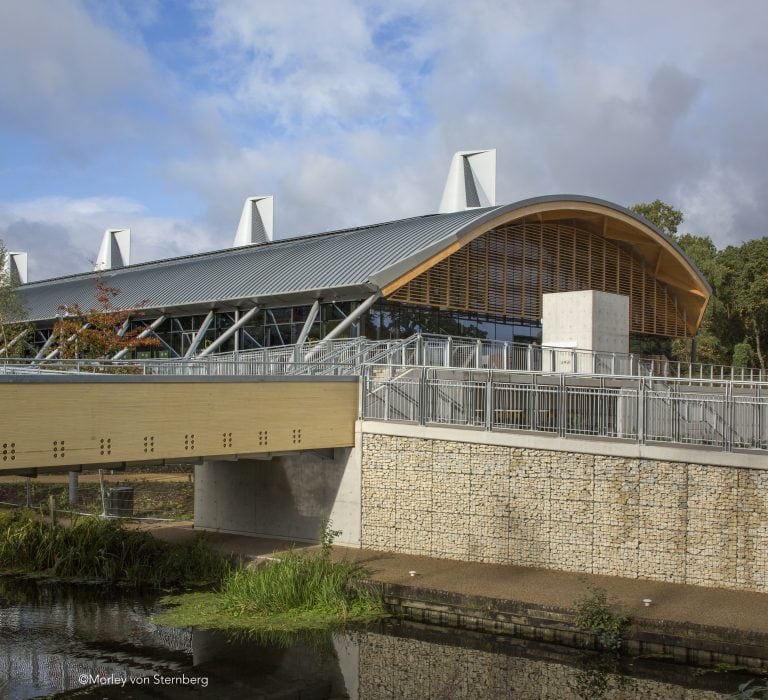
1 Triton Square
Office refurbishment focusing on the circular economy - maximising the retainment and reuse of materials.
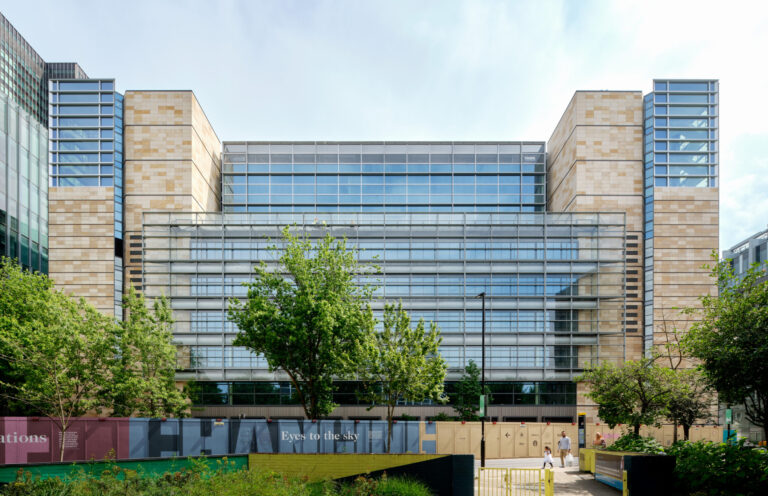