What’s at risk with reuse?
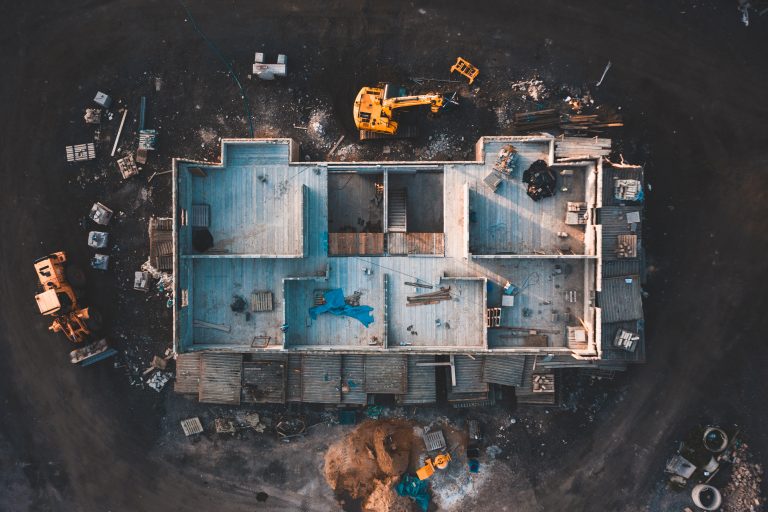
Embracing the circular economy in the built environment requires a paradigm shift and levels of collaboration unparalleled in other industries. Reuse is a crucial pillar of a more circular approach. Apocryphal and anecdotal evidence suggests that a perceived barrier to wide-spread reuse (of assets, components and products) in the construction industry is insurance.
Through a series of interviews with stakeholders at every stage of the construction supply chain, it seems that is not true. The reuse of materials/products/components/assets is not a barrier to getting insurance for a completed asset. Indeed, those in the insurance industry who we interviewed, actually indicated they had never even been asked the question!
The real barrier is risk.
Risk n. the possibility of something bad happening
Construction stakeholders are reticent to reuse assets/components/products unless they know that they will perform at an acceptable level i.e. that they are fit for purpose. Consequently, what happens if something goes wrong and which party carries the associated risk of failure?
New assets/components/products come with warranties providing an established and effective way of managing risk. Assets/components/products that could be reused do not ordinarily come with a warranty and therefore are commonly perceived as too risky to use again.
Interviewees identified the following challenges, which all have associated risks, which are holding back more reuse:
- How is the remaining performance and remaining life assessed?
- How are intangible aesthetic qualities such as “finish” quantified in order to enable reuse?
- If additional assessment/survey work is required to enable reuse, where does the cost burden sit?
- If deconstruction/re-conditioning/re-engineering takes extra time and costs more, where does the programme and cost allowance come from?
- How is damage during removal/re-installation handled? Furthermore, what happens if something is damaged “in transit”?
- How is the reused, “second-life”, performance guaranteed?
- Designing and building with new assets/components/products/materials is perceived as easier, and cheaper, than reused, so what’s the business case for reuse?
- How can designers be sure that second life materials and products will be available once a contractor actually starts procurement?
These questions, which relate to the assets/components/products as well as the actual construction process, were raised consistently all the way along the supply chain, make for a daunting read.
However, all is not lost.
The reuse of demolition arisings, crushed, graded and quality assured for reuse on site, is now standard practice. However, it took 10 years to get to this point. The change has come about because contractors can quantify the risk. Data is now available so that they can look at a built asset and confidently predict the demolition arisings in terms of types and quantities of materials. The cost of certification for certain uses has been absorbed.
Manufacturers are taking back their own products, such as raised access floors, re-engineering and reconditioning them. These are then being sold back into the market for reuse.
Products and materials that have inherent aesthetic properties, such as tiles or floor coverings, are being reused where acceptance criteria can be defined or in areas that are not “on show” to the public.
As good as these examples are, they demonstrate the slow, piecemeal way in which the construction industry is going about embracing reuse (let alone circularity in its entirety) and addressing the risks.
Project teams have an opportunity to make a real difference, and in some instances, reuse has been embraced and the risks managed, but we need a paradigm shift. We all know the construction industry is notoriously slow to change and modernise, what can we meaningfully do now to address this commercial attitude to risk and replace it with a common-sense approach? Answers on a postcard please…
We can’t afford to wait another 10 years for a modest change. We need viable, universal takeback and reuse of all construction materials and products NOW!
Thanks to all those involved in the interviews that have informed this blog and the contributors to the UKGBC Circular Economy Forum Working Group: AKTII, Cleveland Steel, Grosvenor, ISG and Orms.
UKGBC has published implementation packs on reuse and Products as a Service to assist built environment projects adopt circular economy principles.
Related
Using the tools we have to build a circular economy
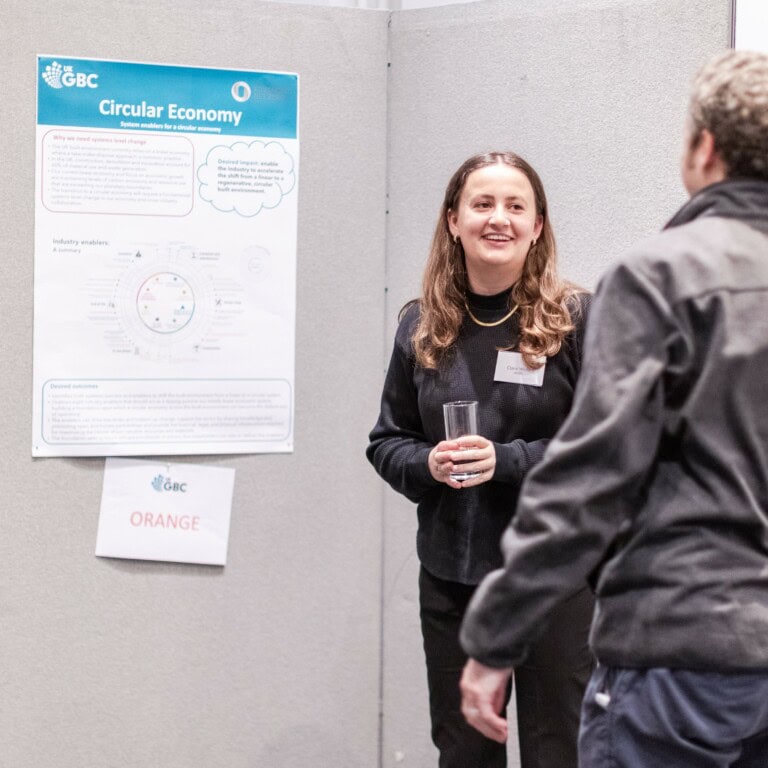
The Do’s and Don’ts for Deconstructability
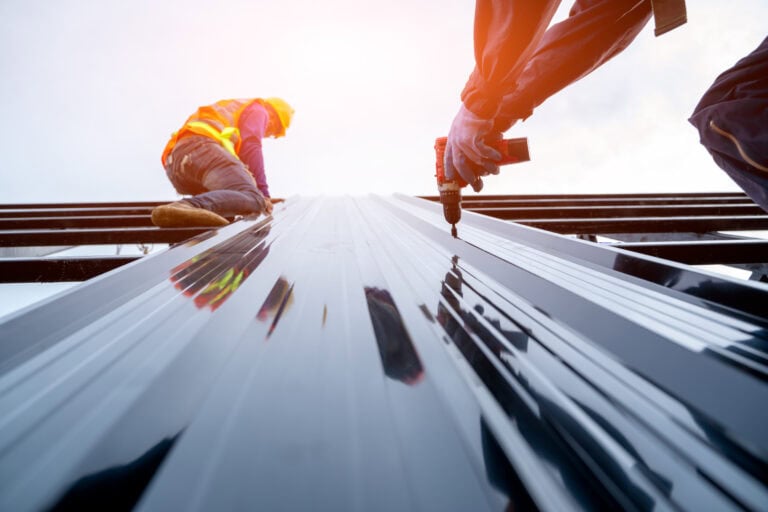
The Challenges and Opportunities of Reusing Steel
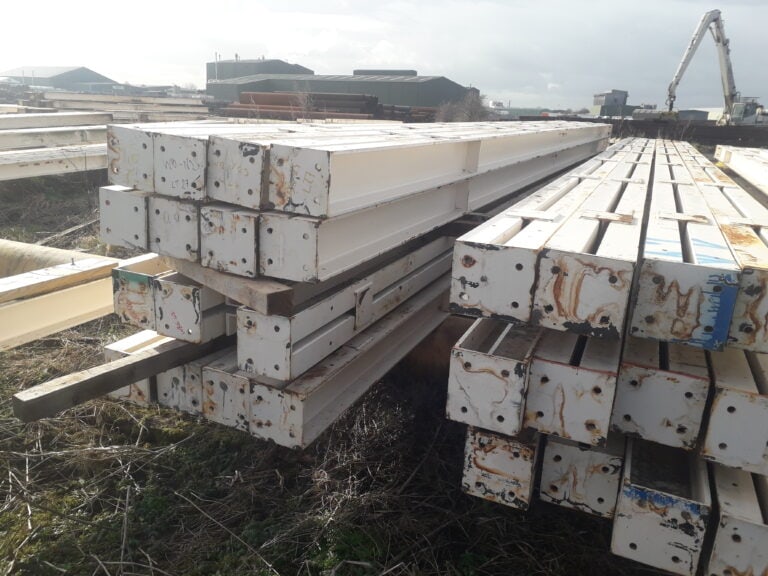
Collaboration and Early Engagement to Enable a Circular Economy: Opportunities and Barriers
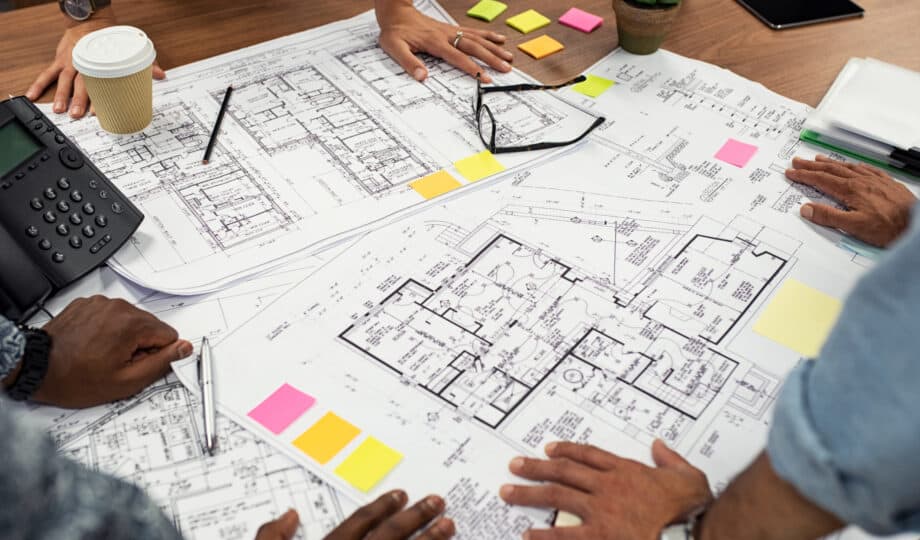