The Do’s and Don’ts for Deconstructability
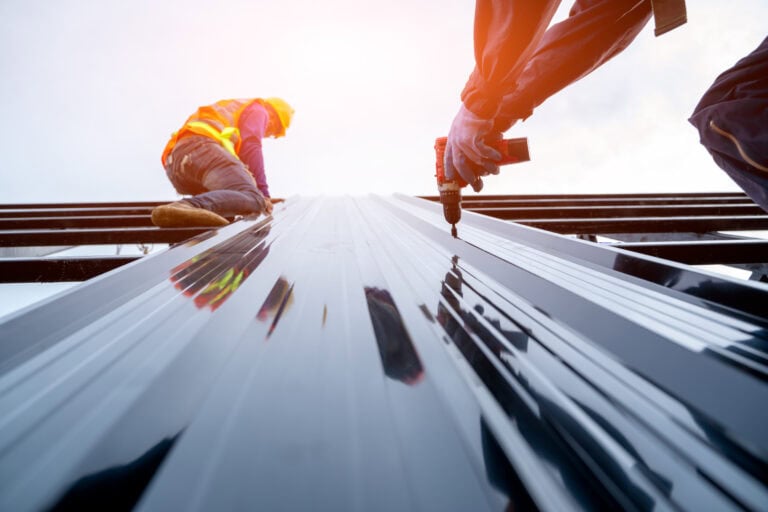
To create a circular economy, a building’s end of life scenario must be considered at its very beginning. The method of construction and the materials used as part of this should be designed so a building can be easily deconstructed, and its component parts reused. This methodology is known as design for deconstruction, or design for disassembly. Why deconstructability? By following this principle, we reduce the demand on raw materials and reduce the embodied carbon of construction.
In this blog post, Sustainability Advisor Kai Liebetanz and the working group from UKGBC’s Circular Economy Forum, share the do’s and don’ts for implementing this principle.
Do
Addressing it early. Embed design for disassembly principles and ambitions early in the design brief within Stages 1 and 2. Retrofitting deconstructability in later stages poses an immense challenge, so it’s best to set guiding principles early on before major design decisions have been made.
Be clear on how to store, update and pass on information. Deconstructing a building at the end of its life requires information. Make sure to collect necessary data on materials, performance where necessary and advice on how to disassemble the element without causing damage. Deconstruction Plans and Material Passports are tools designed to aid that process. This data must be able to be accessed, altered and passed on if ownership changes to make sure it is up to date when the building is facing deconstruction. Those processes should be designed from the outset to make sure they are an integral part of the building’s design and operation.
Understand value of deconstructability. Without a clear understanding of the value and purpose of circularity measures, they are at risk of being taken out during the value engineering process.
Prioritise wisely. Chances are, the building you design will not be fully deconstructable. But that doesn’t mean you should not consider a circular approach for your design. Instead, focus on where you can have impact and prioritise the items with the highest embodied carbon impact or ecological footprint, most likely to be removed and most likely to have reuse potential at end of current life.
Create a deconstruction methodology. Deconstruction is not just reverse construction, it comes with its own processes. It is good practice to develop a deconstruction plan including all necessary information (drawings, sequences) needed for practical deconstruction. It might be a good idea to involve demolition engineers at design stage to aid this process.
Don’t
Use Composite products. Composites might come with good performance credentials, but are almost impossible to separate, reuse and recycle. Instead opt for a building in layers with reversible connections where possible. If you do use composites, make sure the whole unit can be repurposed.
Use chemical fixings, such as glue. Opt for reversible mechanical fixings where possible. Consider how the element can be uninstalled without causing damage either to the element itself or the substructure supporting it.
Neglect recyclability. Apart from the possibility for disassembly, chosen materials and products should ideally also be recyclable. If damage during deconstruction renders a product unsuitable for reuse, recycling offers a fallback route to keep high quality materials in the circular economy. Failure to do so may result in downcycling to lower quality products or incineration. Ensure any coatings applied to elements don’t prevent future reuse or recyclability
Forget to update records. Buildings and their components change over their lifetime. Therefore, records about materiality and deconstruction manuals are likely to be outdated once major refurbishments have happened. Keeping the records up to date and recording maintenance information is therefore vital to ensure a well-managed deconstruction process with minimal destruction to maximise reusability.
With thanks to the members of the Circular Economy Forum for their work on this article, in particular:
- Rachel Hoolahan, Orms
- Steve Gilchrist, Grosvenor
- Ajay Shah, Modulous
- Penny Gowler, Elliott Wood
Related
Collaboration and Early Engagement to Enable a Circular Economy: Opportunities and Barriers
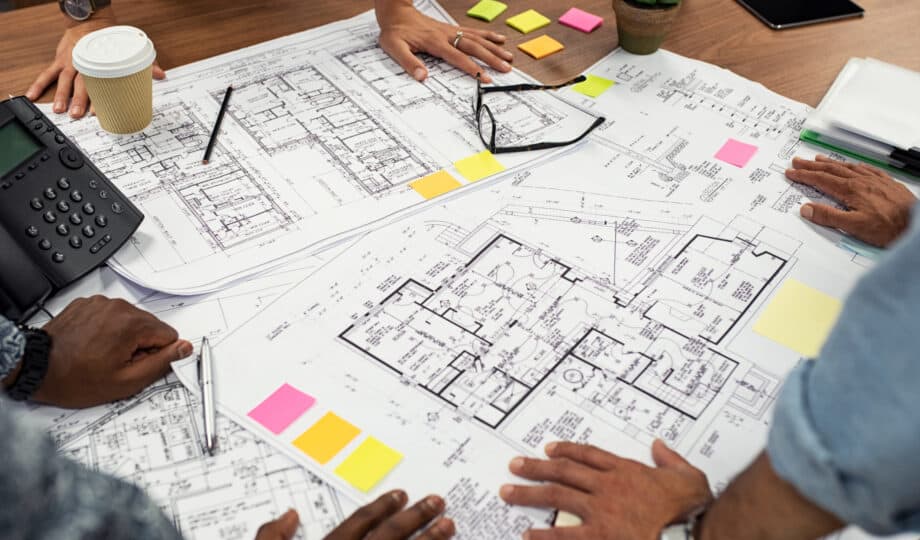
UKGBC launches new toolkit to accelerate the transition to a circular built environment
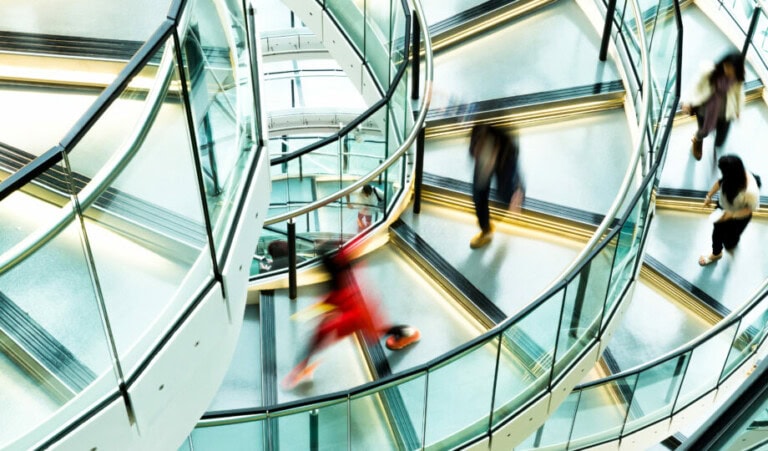
The Challenges and Opportunities of Reusing Steel
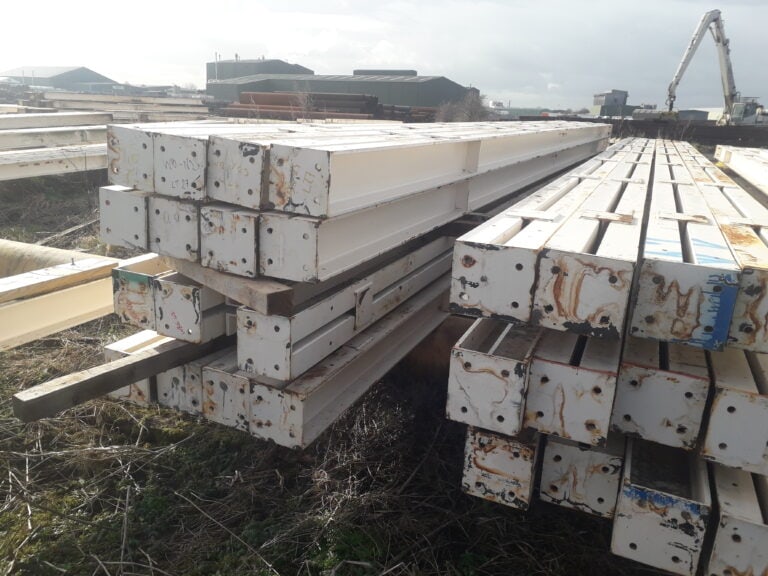
How a Circular Economy Can Fight Biodiversity Loss
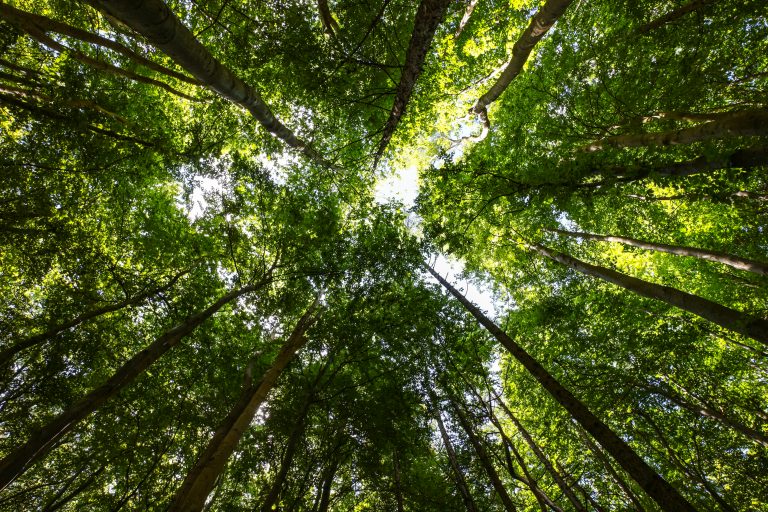