Martlesham Training and Office Building
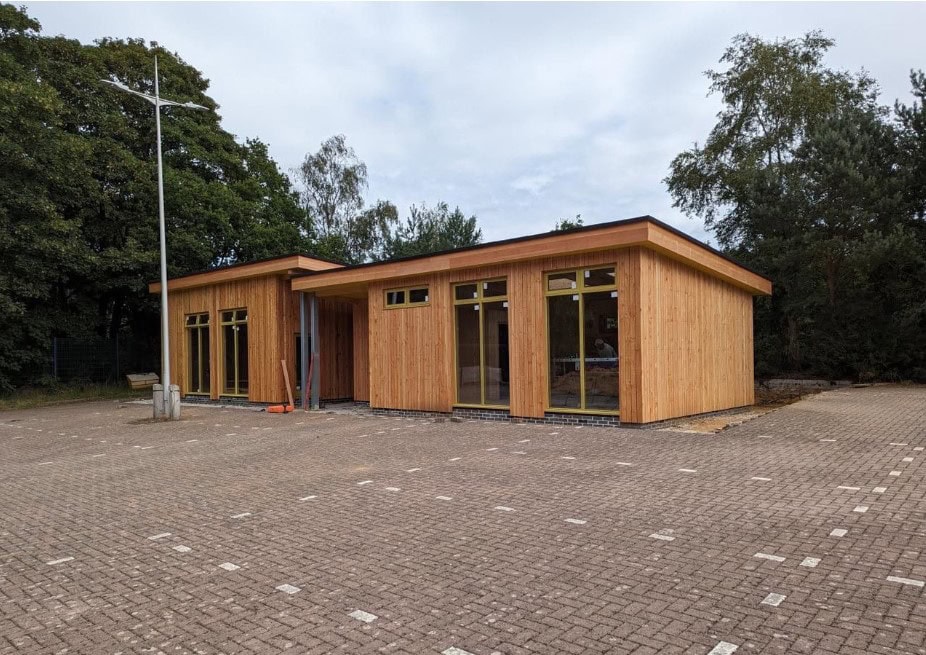
Key Sustainability Objectives/ Outcomes
Embodied Carbon
The superstructure of the Martlesham project uses entirely natural regenerative materials including LVL roof beams, wood-fibre insulation, timber joists, hemp fiber insulation bats, and vertical Douglas Fir rainscreen cladding. Additionally, the building’s estimated Life Cycle Assessment (A1-A5) is only 219kg Ce/m2 with biogenic carbon estimated at 1.36 tCe/m2 resulting in a net -1.139 tCe/m2. The wall cassettes used in the building require no primary structure up to 3 stories, but the system allows for the later integration of an LVL frame for vertical extension up to 8 stories.
Resource Use and Circular Economy
Natural Building Systems manufactured the cassettes used in the Martlesham project with Design for Deconstruction and Design for Adaptation principles in mind. Their standardized building system allows for rapid site assembly using timber spline pegs. This assembly method allows for the potential to re-configure and re-use individual cassettes and components during the service life of the building, and ultimately disassemble and re-use the entire building elsewhere. The building’s superstructure also allows for disassembly and adaptation by using pre-manufactured components, while the substructure uses compacted hardcore recovered from the site area. Off-site production using digital design and manufacturing tools optimizes material efficiency and reduces waste.
Operational Energy Performance
The HempSil bio-composite and hemp-fibre insulation used in the Martlesham project allow high levels of thermal and vapour buffering, reducing the risk of summer overheating and improving indoor air quality. The building’s estimated Energy Use Intensity (EUI) is only 60 kWh/m2 per year.
Lessons Learnt
Martlesham was Natural Building Systems’ first project undertaken as a nominated supplier, working with a main contractor. It was necessary for them to agree to a very short lead time to meet the client’s funding timetable. Detailed design was not fully developed prior to manufacturing the components resulting in manufacturing errors in a number of bespoke elements, causing delays in delivery.
Lesson learnt: A realistic lead time for design development prior to manufacture is critical to managing timelines, especially when working with third party contractors who require certainty on delivery dates.
The main contractor chose to employ skilled carpenters to carry out the assembly. This was not necessary and resulted in avoidable additional costs, since the system is designed for assembly by non-specialist labour.
Lesson learnt: Natural Building Systems’ site supervision and assistance would have been more effective with some initial training provided to non-skilled operatives.
The contractor had limited insight or interest in Natural Building Systems’ wider sustainability goals, in particular around the need for circular economy construction solutions, leading to misalignment in values and objectives.
Lesson learnt: Natural Building Systems found that they need to devote more time and resource into explaining the sustainability advantages of using an off-site manufactured, bio-based and circular construction system, but also the inherent challenges of this approach.
In summary, four key lessons have been learnt for future projects:
- Allow sufficient time to develop detailed design prior to manufacture.
- Invest more resources where possible in professional CPD about the building system for contractors on site, ahead of site installation.
- Develop collaborations with contractors who share a similar sustainability ethos where possible.
- Provide more comprehensive site supervision so questions can be answered quickly, ensuring better build quality.
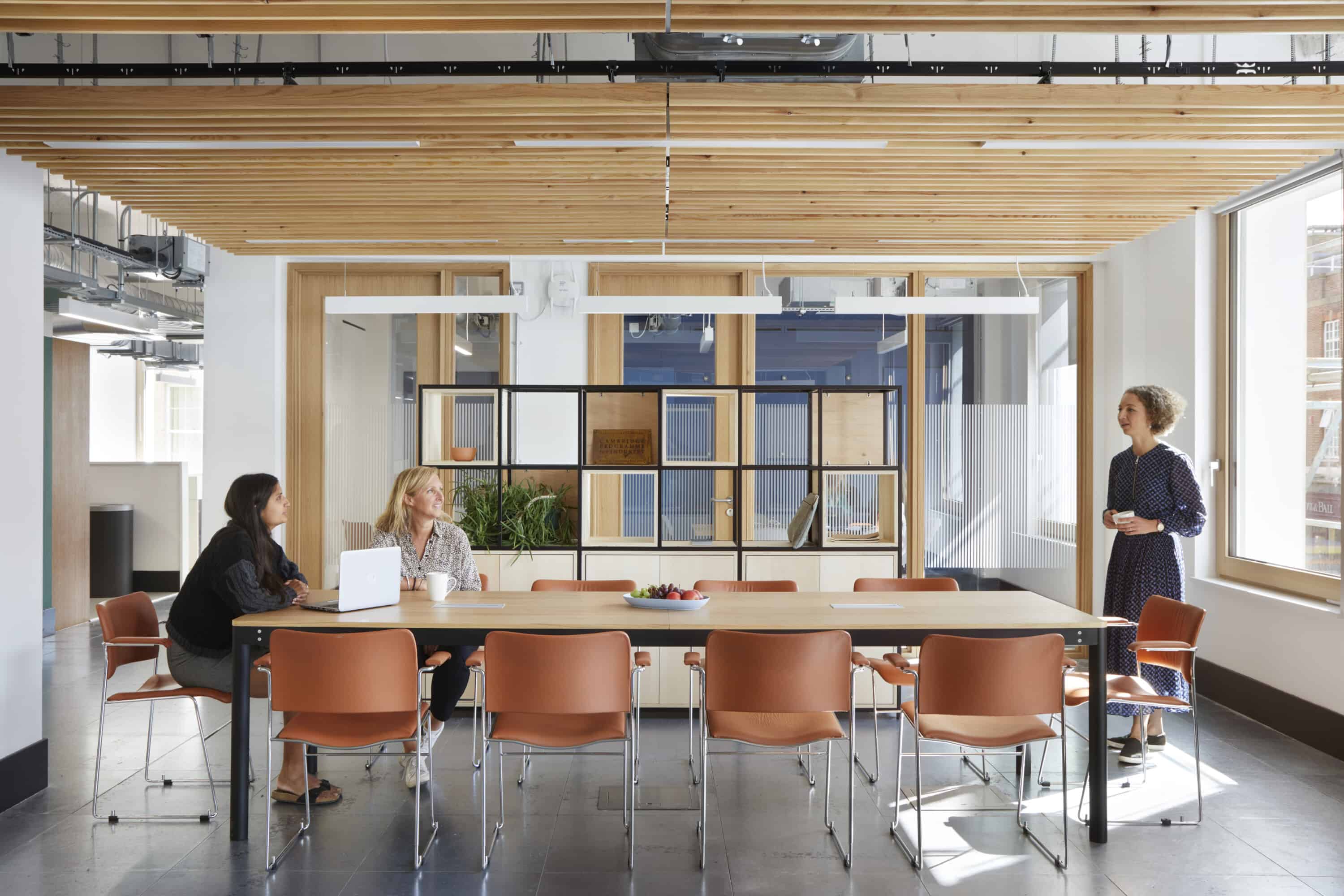
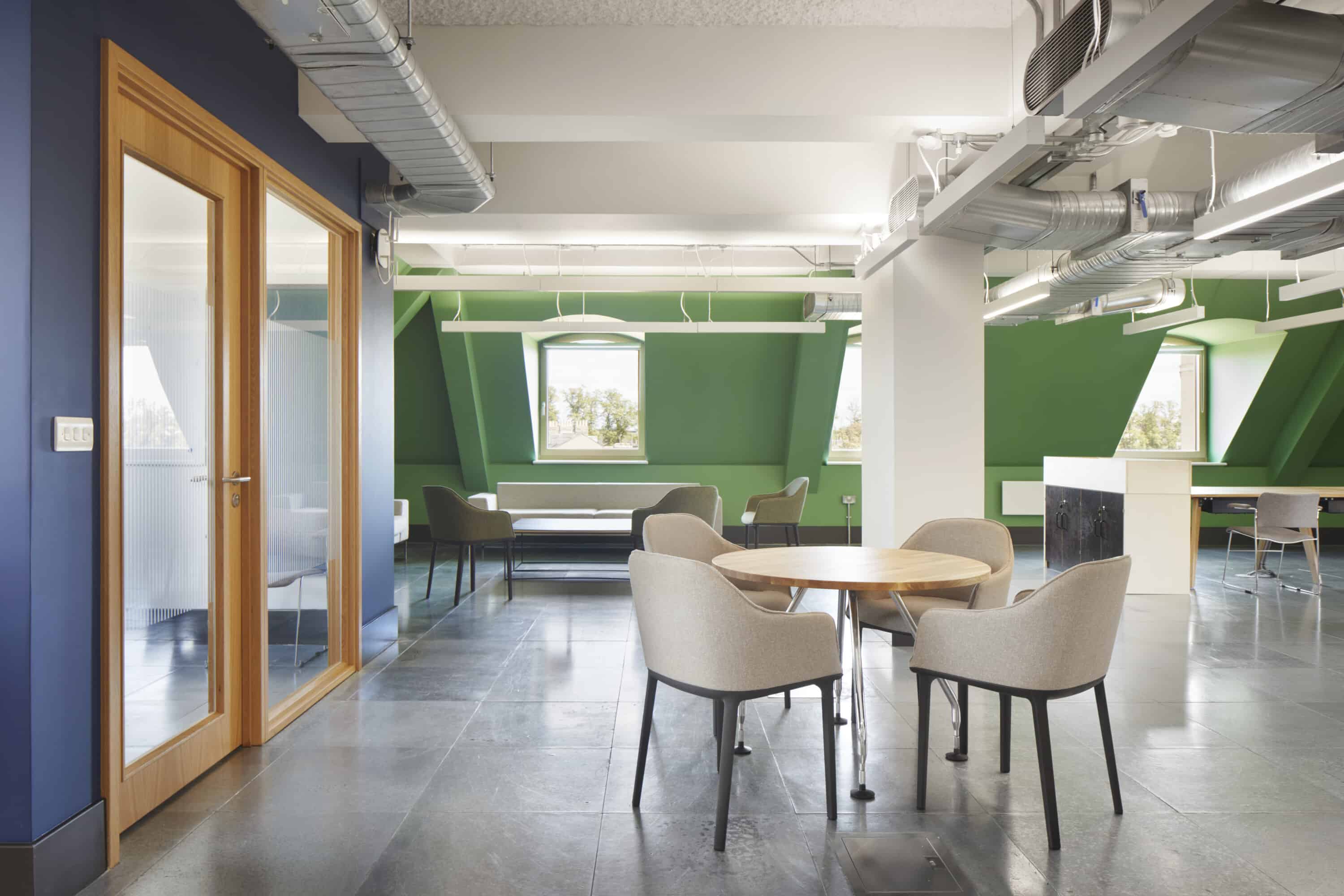
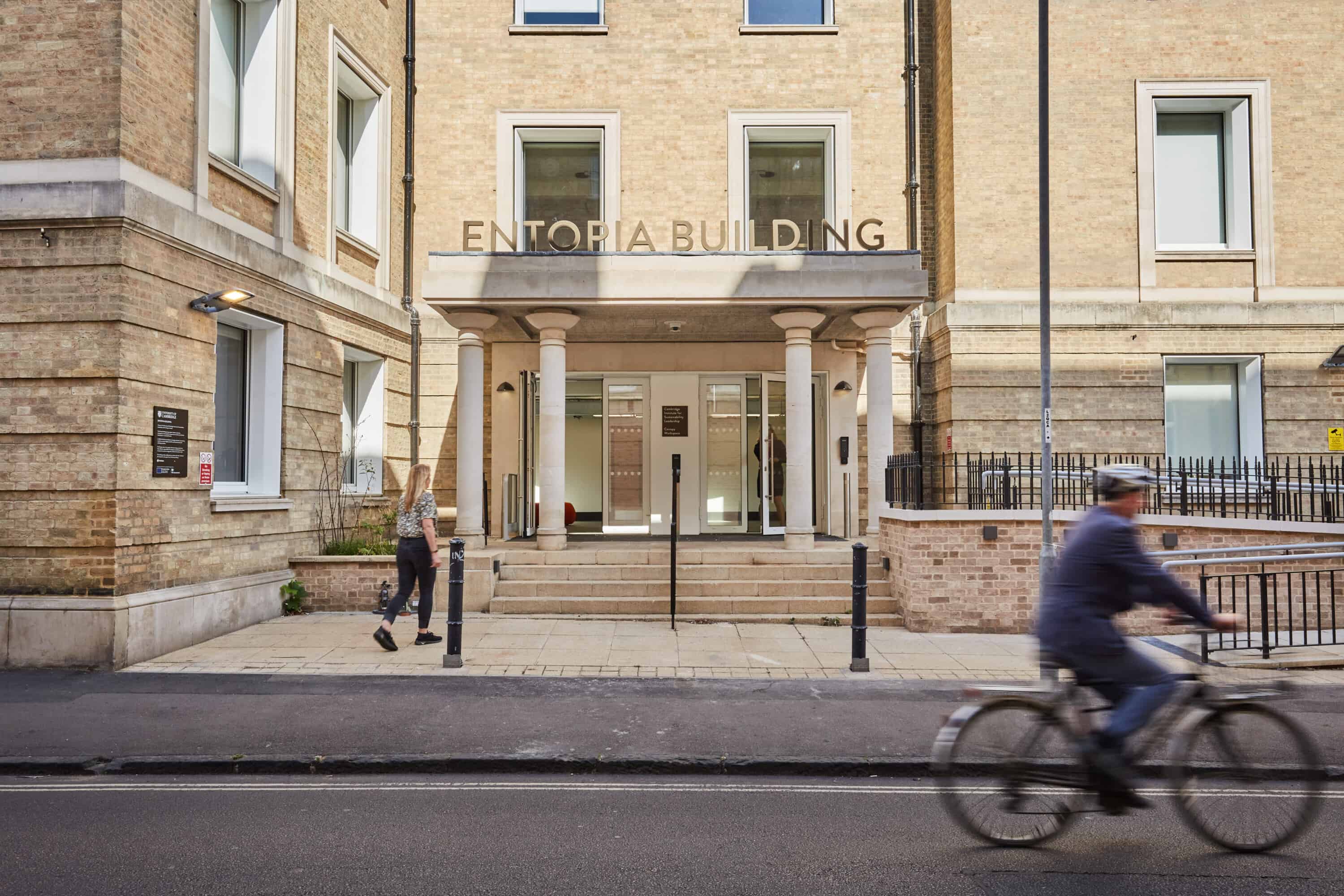
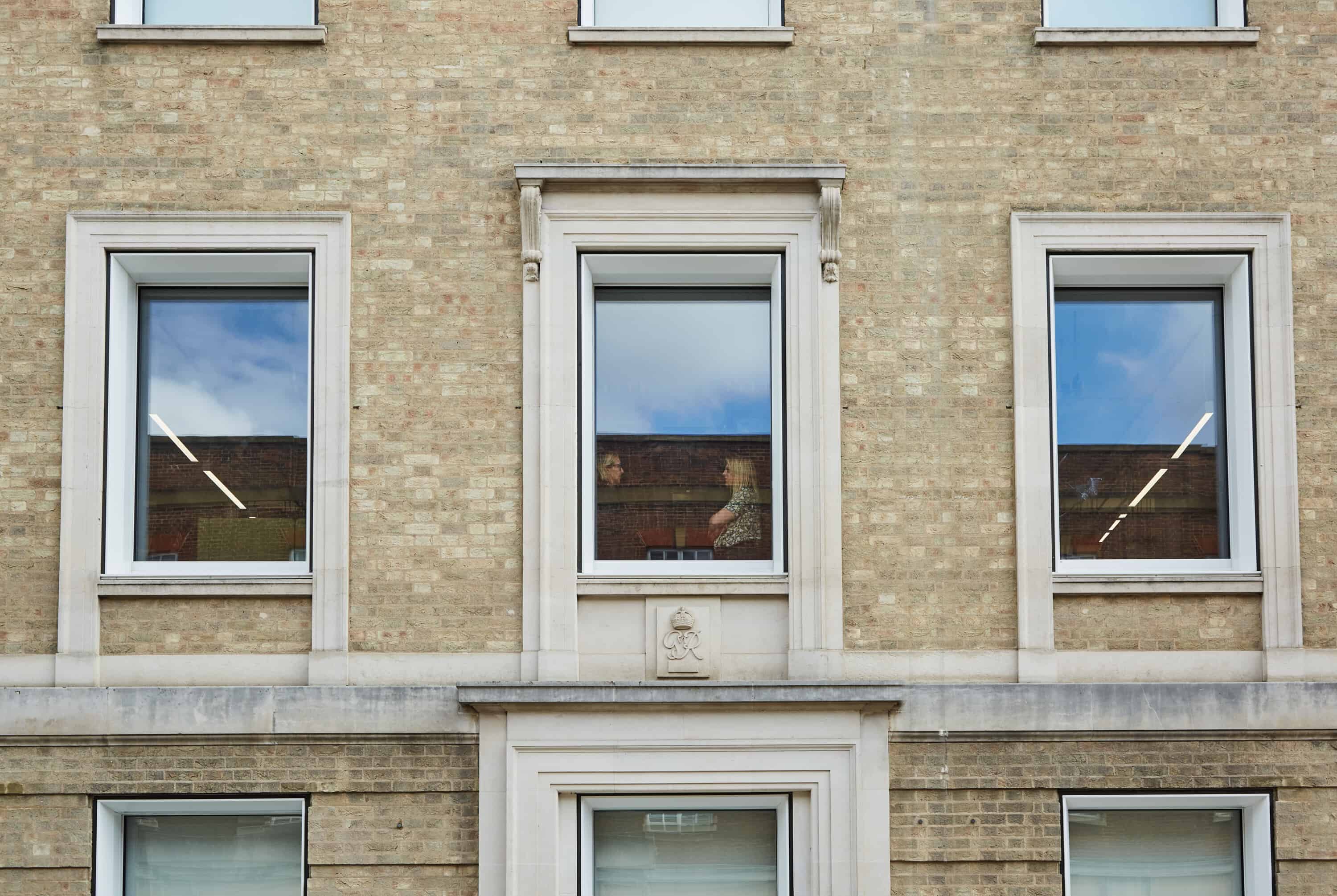
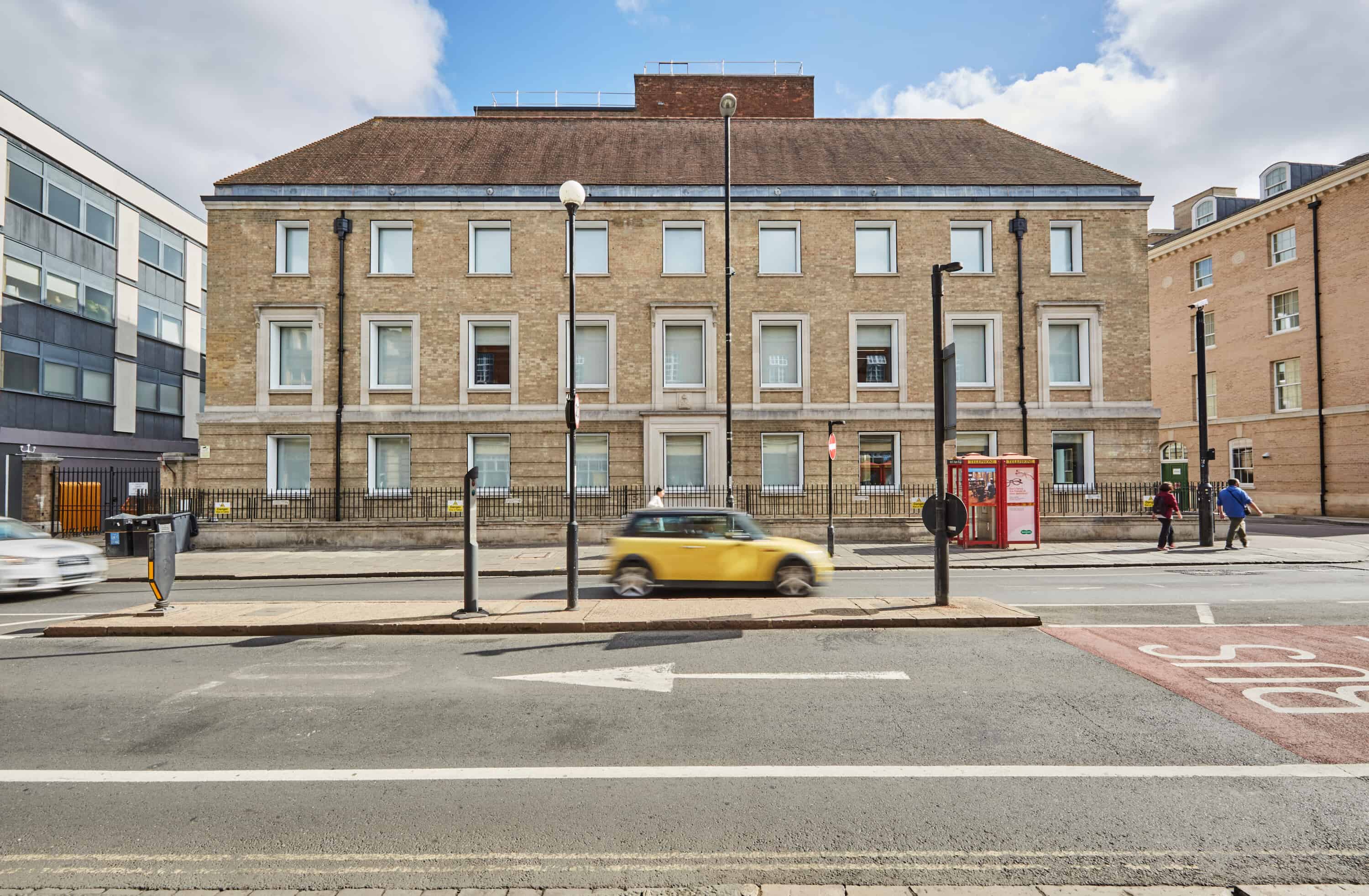
Related members
Related
Kintyre
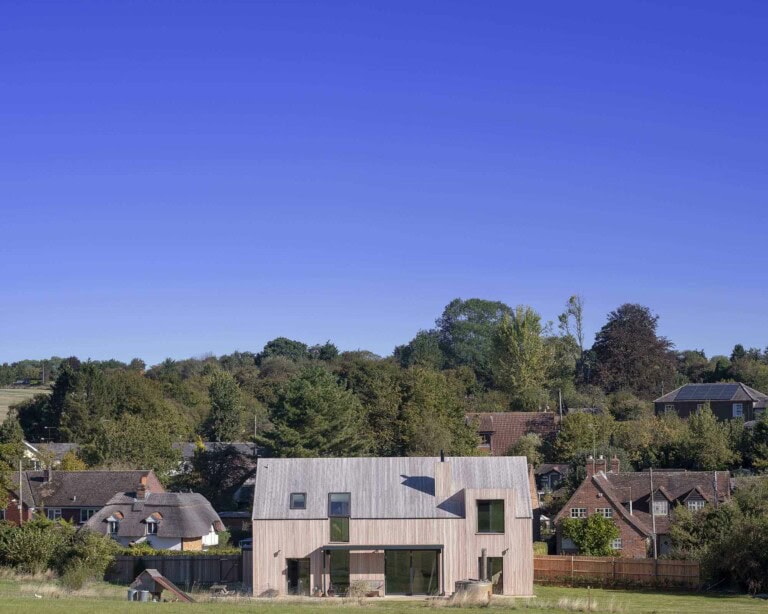
20 Water Street
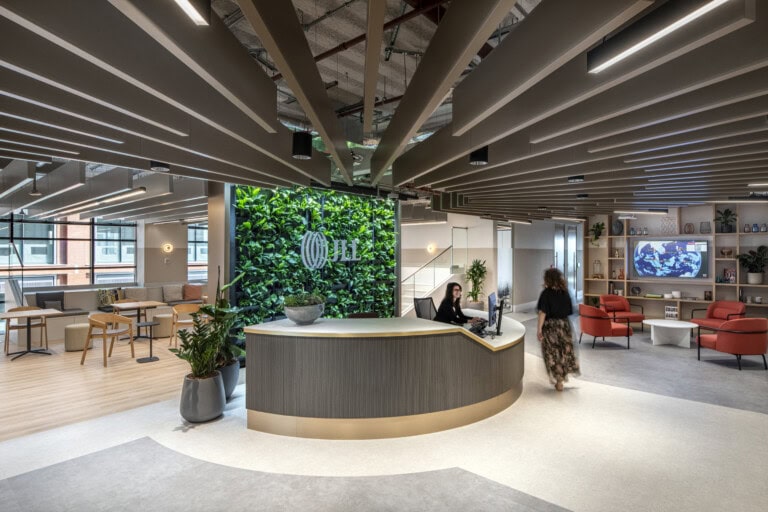
JLL – Manchester office fit-out
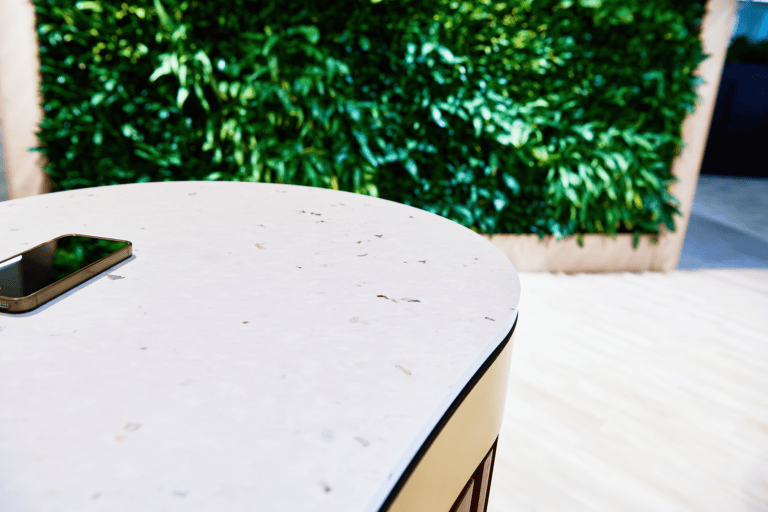
Cambridge Avenue
