The Risby
An energy positive home generating three times more energy than it uses, built using modern methods of construction.
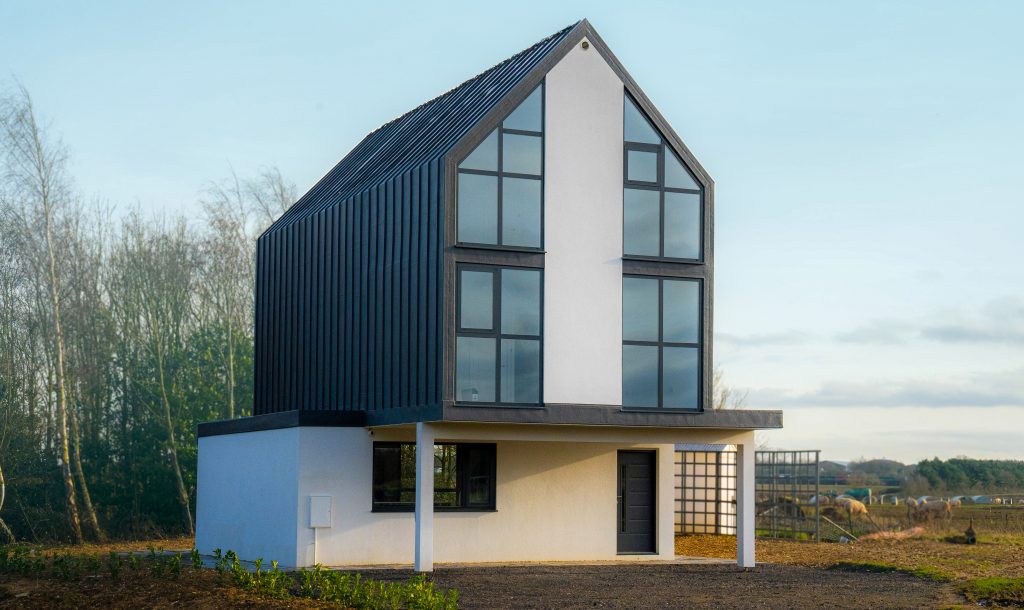
Highlights
- Under average load and climactic conditions, 4,000 kW h per annum is all that the Risby needs for internal and external lighting, space heating and domestic hot water.
- U–values for floor, walls, roof, windows and doors far exceed the Concurrent Notional Dwelling Specification and Limiting Fabric Parameters, specified in Building Regulations approved document L1A. The values expressed in in W/(m2K) are as follows: floor 0.12, walls 0.14, roof 0.12, windows 1.00 and doors 0.9.
- With air permeability of 2 m3/(hm2) at 50 Pa and 10,000 kW h per annum of renewable energy generation from integrated solar tiles, the overall Target CO2 Emissions Rate is easily surpassed.
- The integrated meters and smart home technology measure the on–going operational performance of the building in real time reporting back to the EPA.
- Over the next 12 months, Grid2.0 will commission an independent report to verify the embedded carbon credentials of the building. This will include a Lifecycle Assessment.
Approaches Used
- Risby is manufactured off–site, adopting modern methods of construction. It is made primarily from engineered timber, which is durable, sustainable, structurally reliable and dimensionally stable.
- Grid2.0’s construction methodology embraces a “pods and panels” approach where MEP is factory installed into three-dimensional pods and two-dimensional panels which make up the internal and external wall, floor and roof elements.
- The construction palette consists of large format CLT and OSB panels (up to 18 metres in length), engineered joists, closed cell rigid polyurethane and aluminium doors and windows.
- The 2D/3D approach to construction provides the foundation for scalable production, which is the stated goal of Grid2.0.
Lessons Learnt
The Risby was built as a prototype, specifically to test and learn lessons from the construction process required to build a new home of this standard, with all the associated process risks inherent with off-site construction. Ultimately, the key lesson was to establish the cost of building to this specification.
In summary, we found that:
- The pods and panels – or 2D/3D building model – can substantially improve the speed and cost of new buildings.
- BIM led design is an important pre–cursor to a smooth construction process.
- BIM literate production teams enjoy the process and complete tasks quickly.
- The net cost of the building is lower than a traditionally built alternative – in all departments: design, labour, materials and overheads.
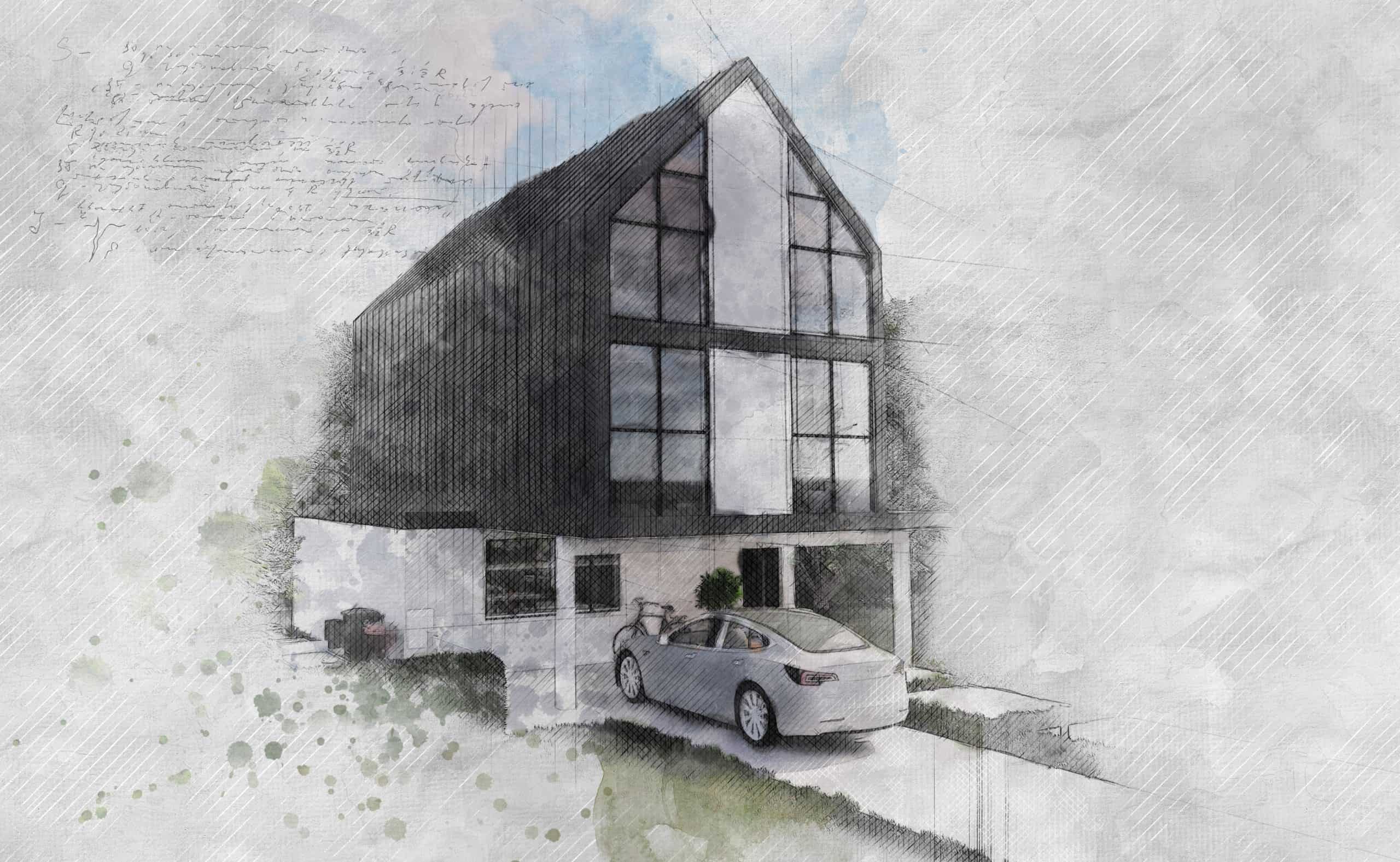
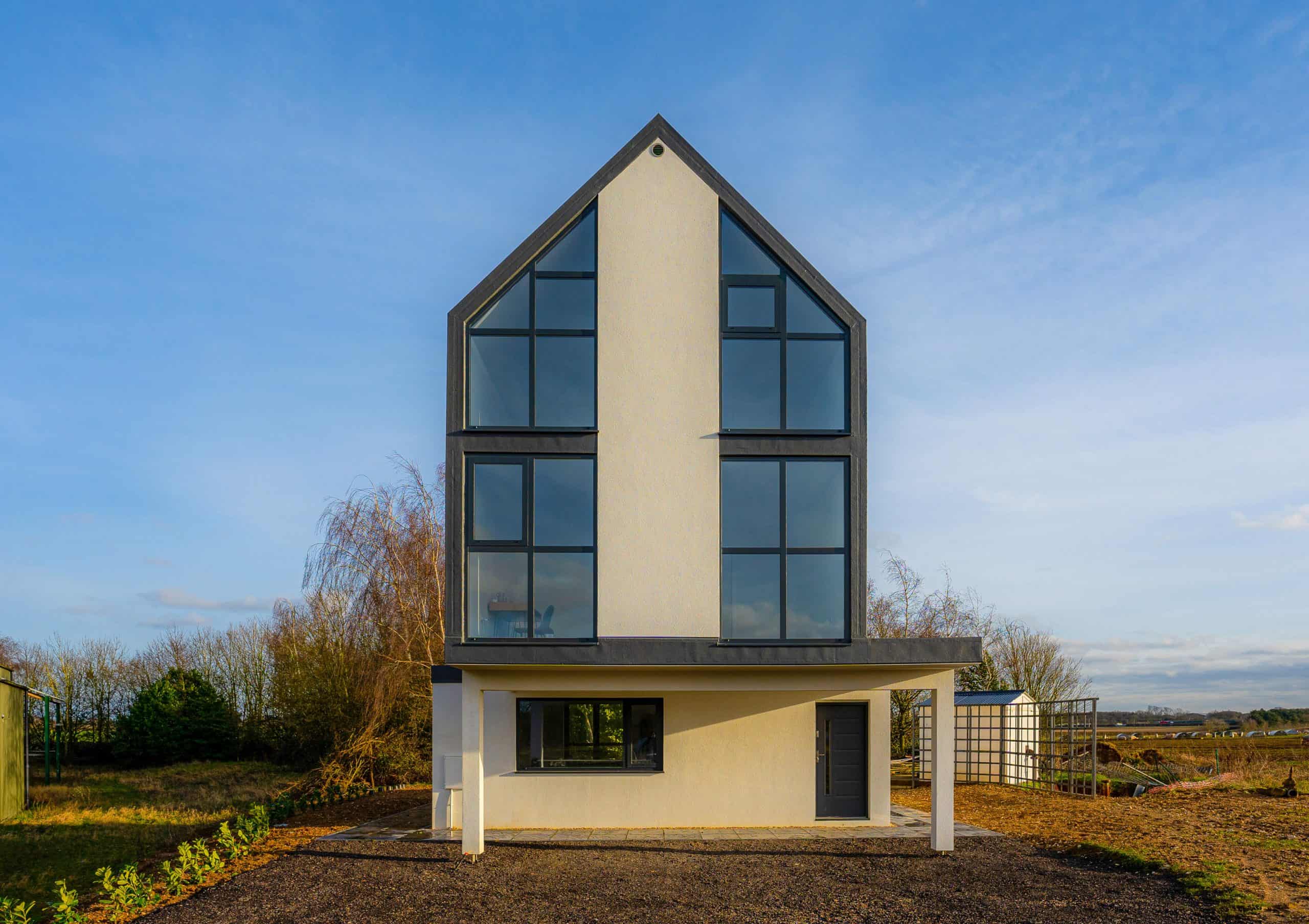
Related
Holbein Gardens
Grosvenor's first office development on track to achieve Net Zero Carbon.
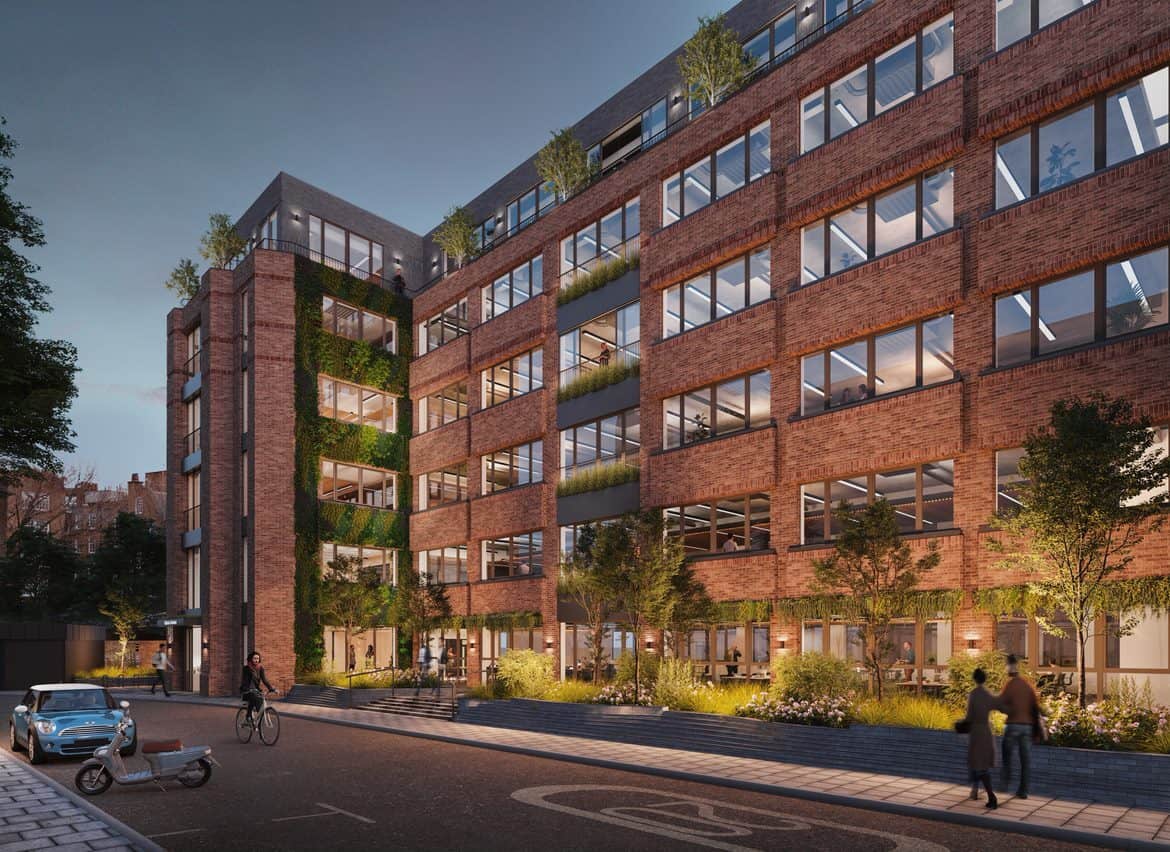
80 Charlotte Street
Mixed-use, all-electric, scheme striving for reduced embodied and operational carbon.
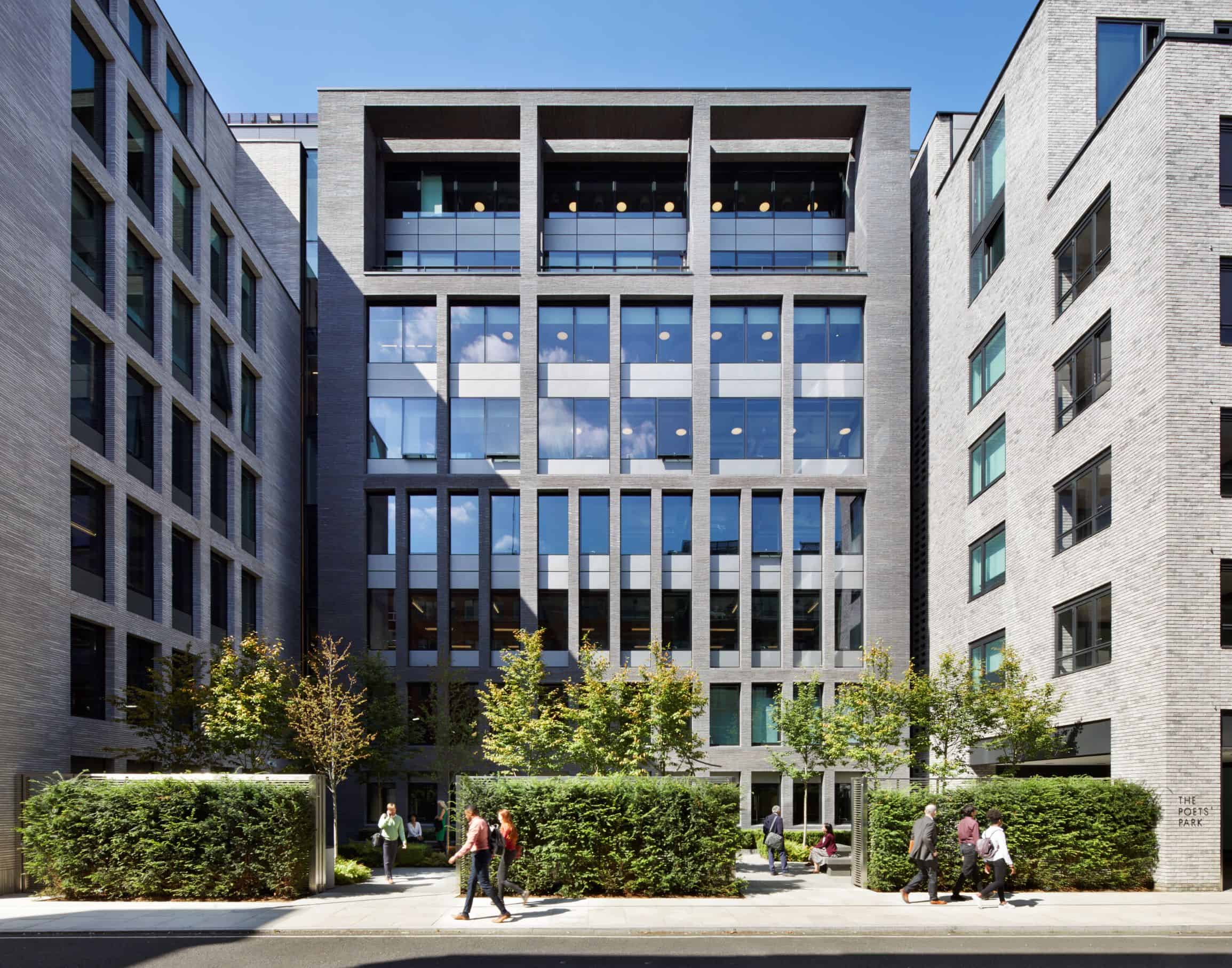
Blackrock Street Housing, Manchester
Net Zero Carbon social housing scheme.
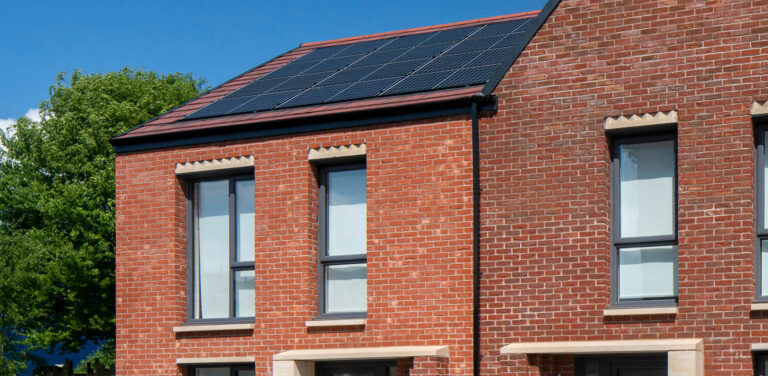
Dorset House
An energy positive house in Dorset that has been built to Passivhaus standards and recycles rainwater on-site.
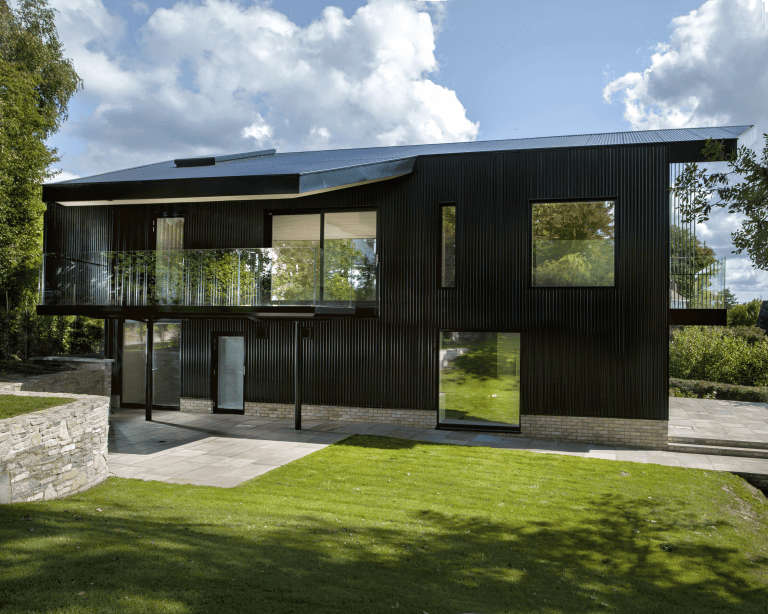