Bio-based Prefab Modular Building System
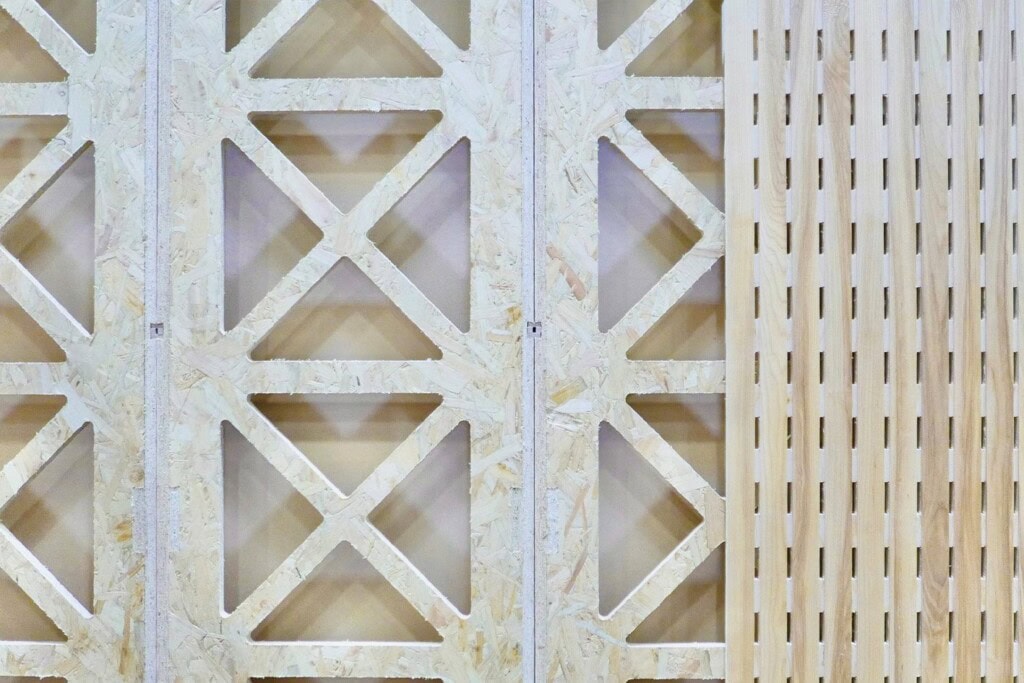
Problem Addressed
The 2019 Global Status Report for Buildings and Construction published by IEA found that the manufacturing of building components and materials is responsible for 11% of global carbon emissions. These emissions are a significant proportion of the built environment’s embodied carbon. When also factoring in operational carbon and the substantial amount of waste generated by the construction industry, the materials and methods we use to construct our cities and homes must be radically reimagined to reduce the environmental impact that buildings currently incur.
Case Study
Green Light Trust (GLT) provide training and support for people suffering mental illness, near woodlands and forestry environments. Natural Building Systems were commissioned to design and manufacture the wall and roof elements for a new building, in an under-used car park adjoining woodland near Martlesham, owned by Suffolk County Council. The 100m2 scheme is comprised of two separate buildings linked by an external walkway. One half will serve as a training facility while the other, offices for GLT. Having already obtained planning permission, Natural Building System worked closely with the client’s team to optimise the design to deliver a breathable, low-embodied carbon, circular solution.
The building was partially completed in August 2023 and GLT are now fundraising to finish internal works including MEP services. The alignment in values between Natural Building Systems and Green Light Trust was manifest in the use of entirely natural, regenerative materials to create a high performing, healthy building.
Excluding biogenic carbon, the whole building LCA for A1-A5 is provisionally estimated at only 219kg Ce/m2 pending completion of the fit-out works. Due to the use of primarily natural materials, the biogenic carbon captured during their production accounts for 1.36 tonnes Ce/m2. The superstructure of the building uses entirely natural regenerative materials and is built with pre-manufactured components to allow for disassembly and adaptation. GLT’s focus on Whole Life Cycle carbon impacts (rather than simply operational carbon) informed a design that limited U Value targets in the building’s roof, walls, and floor to 0.18W/m2K, 0.2W/m2K, and 0.18W/m2K respectively while the estimated Energy Use Intensity (EUI) is estimated at 60kWh/m2 per year.
Additional information about this case study can be found at the link below.
Facts and Figures
This page presents data, evidence, and solutions that are provided by our partners and members and should therefore not be attributed to UKGBC. While we showcase these solutions for inspiration, to build consensus, and create momentum for climate action, UKGBC does not offer commercial endorsement of individual solutions. If you would like to quote something from this page, or more information, please contact our Communications team at media@ukgbc.org.
Related members
Related
Sustainable Structural Insulated Panels
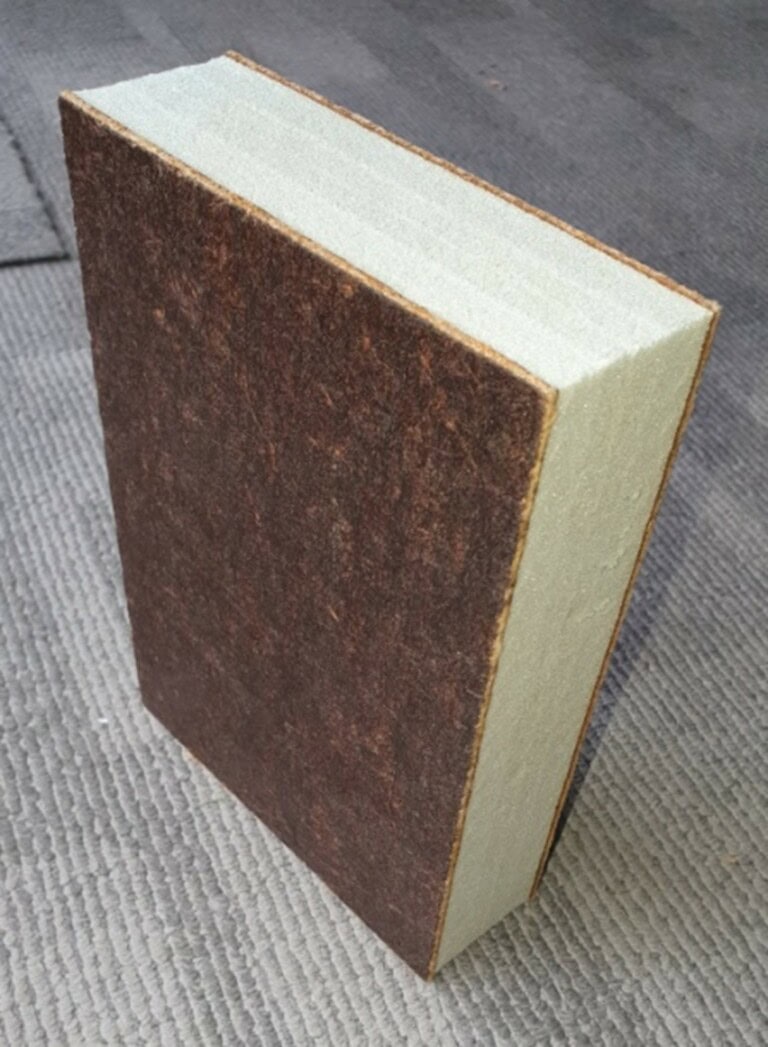
Bio-based modular wall system made of timber and straw

Insulation boards made from meadow grass
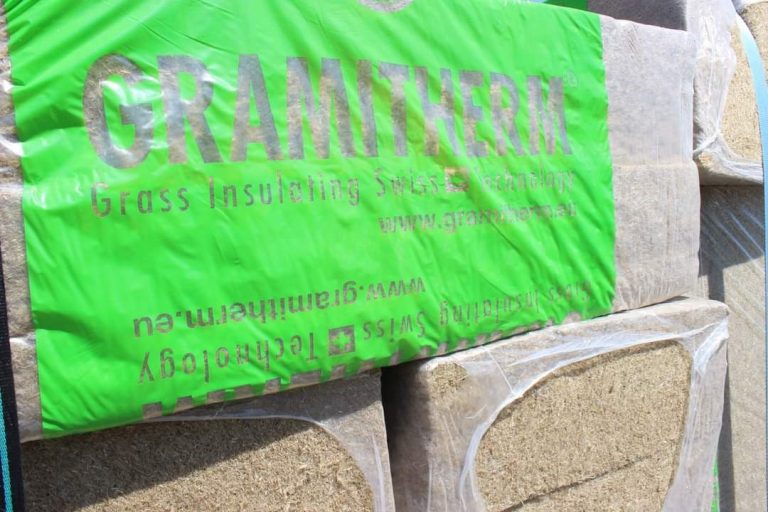
Mycelium insulation
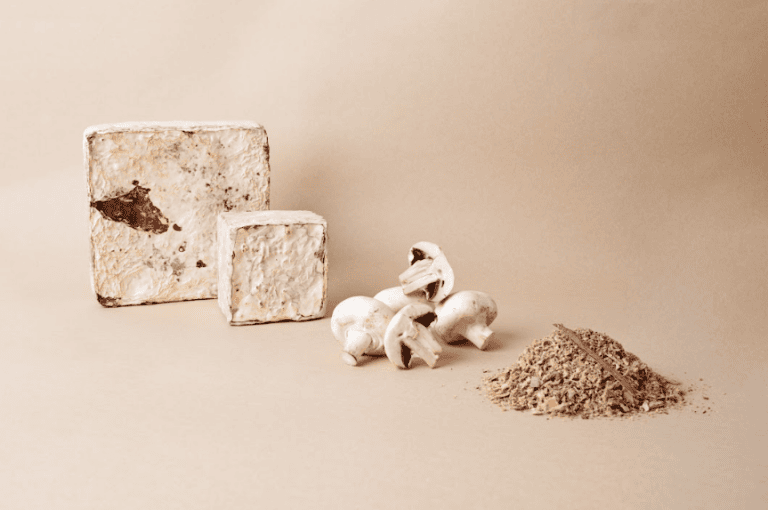