A second-hand materials market: The next chapter in construction’s sustainability story
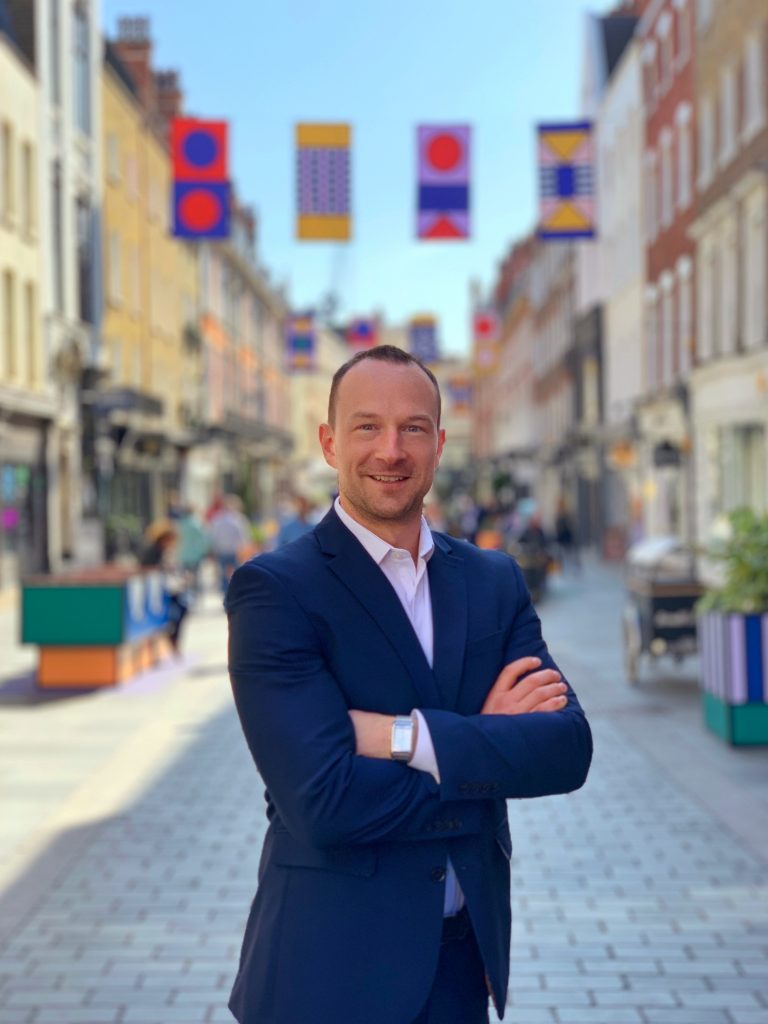
It feels like the construction industry has got its head around embodied and operational carbon, and the large volume of waste we generate in development.
But the thinking still appears to be on driving reductions through optimising new construction, with new materials. Insufficient attention is given to the Circular Economy Principle of Material Re-use.
The next chapter in the construction sustainability story is carbon reduction through asset and material re-use, but there are many challenges to overcome. My involvement in the UKGBC Circular Economy Forum and leading one of its Working Groups has really opened my eyes to the possibilities of a second-hand market.
I could list all the blockers and reasons why we think this is too difficult. Instead, I want to explore the idea that projects (the buildings we construct) are just part of a wider lifecycle – we need to break the habit of designing and constructing them as one-offs, giving insufficient consideration to how they and their parts are manufactured, come together on site, treated during use and at the end of their life.
Changing this is a huge challenge, but one we must face given our voracious urban consumption habits. How does one design and construct a building knowing what will happen in the future? What happens as tenants come and go, as technology changes, when it is sold or transacted, when repairs and maintenance are carried out?
Take a moment to imagine how much easier things could be if buildings were designed to be disassembled: if all the elements were all tagged with readily accessible data, where the materials no longer needed for this building are simply removed and re-sold on a second-hand market.
We need to put ourselves in the mindset of being the custodian of a piece of land or volume of space, making decisions with the long term in mind. Often this long-term thinking may come at a cost – it is all too easy to do things quick and cheap in the now. The value of such sustainable decisions will need to be recognised by the industry to balance this investment. And there is growing evidence of consumers, tenants and investors searching out and paying a premium for sustainable products, just look at B Corps. Long term, informed thinking now will pay off in the future.
Improved information handling is one of the keys to unlocking the circular economy in construction – if we understand things better, we will be much more likely, and able, to re-use them.
The end of construction is the best snapshot we have of what makes up a building, however that information is not widely collected, formatted and stored in appropriate ways for long term use and it is rarely updated. This diminishes its accessibility and critically the trust in its accuracy – why bother looking for something if you don’t expect to find it… isn’t it easier to just figure it out from scratch, or just rip things out and start again?
If we design and construct for disassembly now, and hold and preserve useful data, we will drop into the circular economy and find it so much easier to re-use materials in the future. Ultimately it will save money and carbon, but we must play the long game. Whether a fit-out for a 10-year tenancy, or a full building development with life of 60+ years, we should adopt the same approach.
BIM and data management have a big part to play in this. Physically tagging building elements in-situ and having digital twin models will allow re-use to become more widespread. One major challenge will be the usefulness of this data through time, as new software and technologies emerge, but we must adopt the retain it and maintain it attitude.
A custodian with a long-term mindset would also be willing to explore design philosophies that better allow the re-use of materials. We strive for optimised and efficient design, with thicknesses challenged down to the millimetre as we focus on maximising NIA… always seeking ‘traditional value’. But this value is short-sighted, one dimensional and backward looking.
Future design should be more flexible in its specification to allow a range of materials sourced on a second-hand market to be used. In time we will finesse our understanding of the value trade-off between these competing approaches, but carbon will be at the centre of it all, and surely re-used is better than new?
We are all custodians of the spaces we live and work in. It’s time our industry started seeing ourselves as such.
At Grosvenor we’re looking to address the challenges presented in this blog, find partners willing to share information and explore a process for materials reuse in London. And we’d like your help.
The first step couldn’t be simpler. Whether you are a client, contractor or designer, help us understand your drivers by filling out this simple survey on materials re-use. Just 5 minutes of your time could advance the market enormously.
Click here to fill out our quick survey: https://us4.list-manage.com/survey?u=cf45e8ba02c74ab23a936850d&id=f76a645f75
I’d like to thank the other contributors to the UKGBC Circular Economy Forum: ISG, AKTII, Cleveland Steel, Orms, WSP, Mott MacDonald, Jacobs and our research partners on the survey including Orms, HETA architects, ElliottWood, CIRCuIT and ARUP.
Related
Collaboration and Early Engagement to Enable a Circular Economy: Opportunities and Barriers
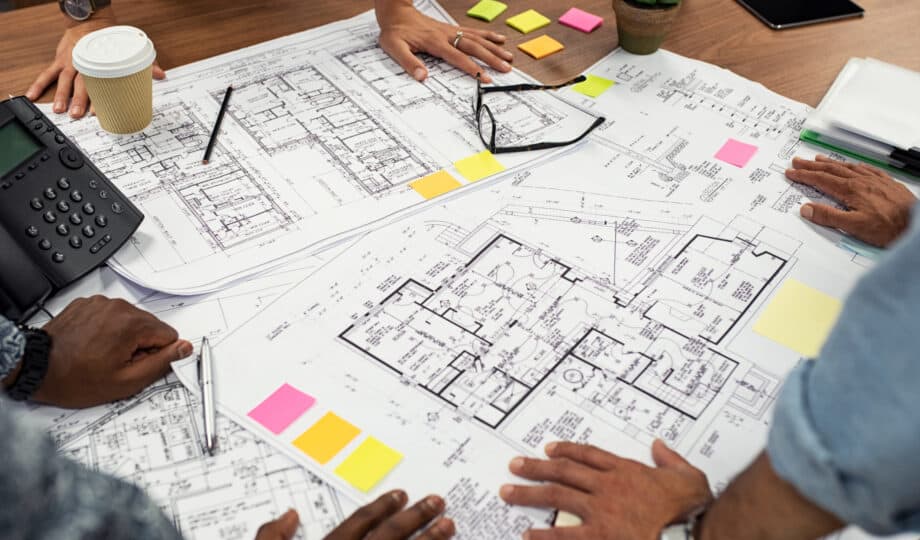
Defining Reuse: Why adopting ISO definitions will help encourage circularity

The Challenges and Opportunities of Reusing Steel
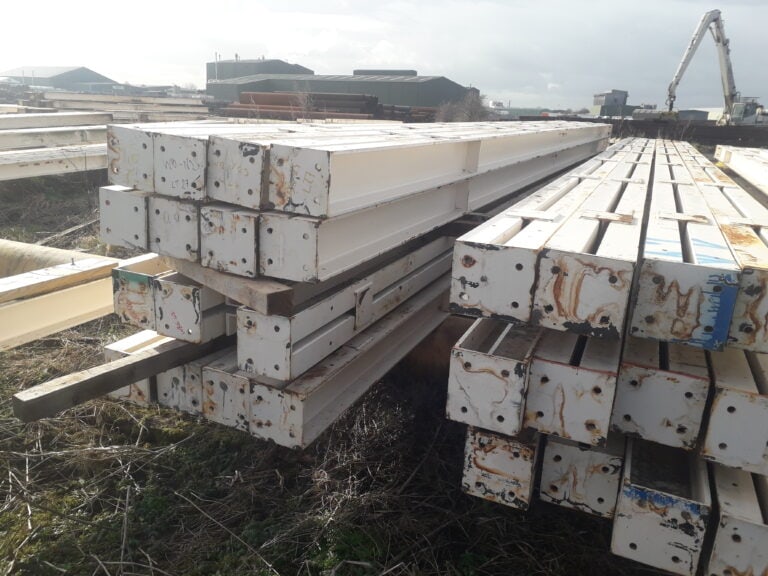
Using the tools we have to build a circular economy
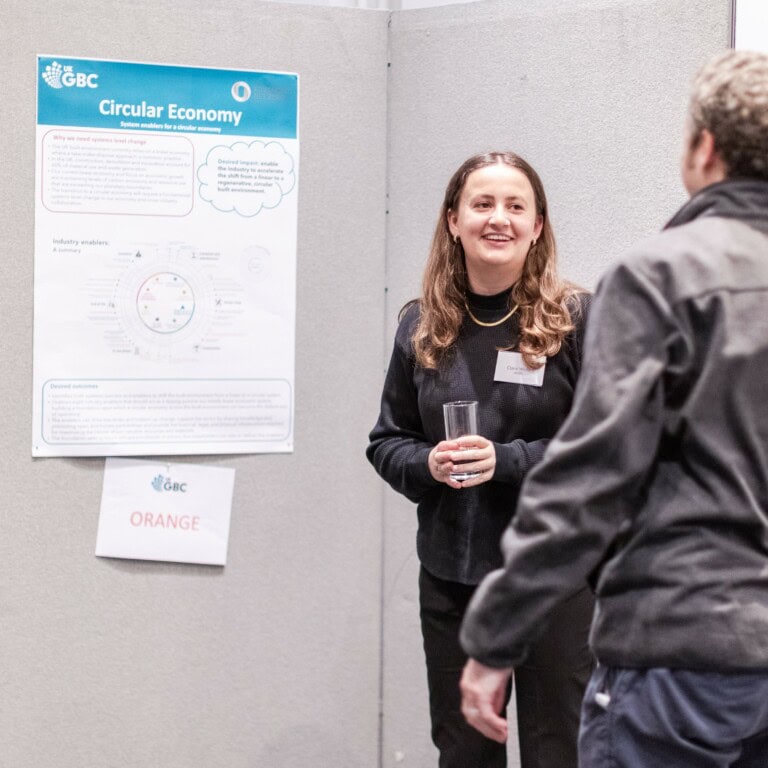