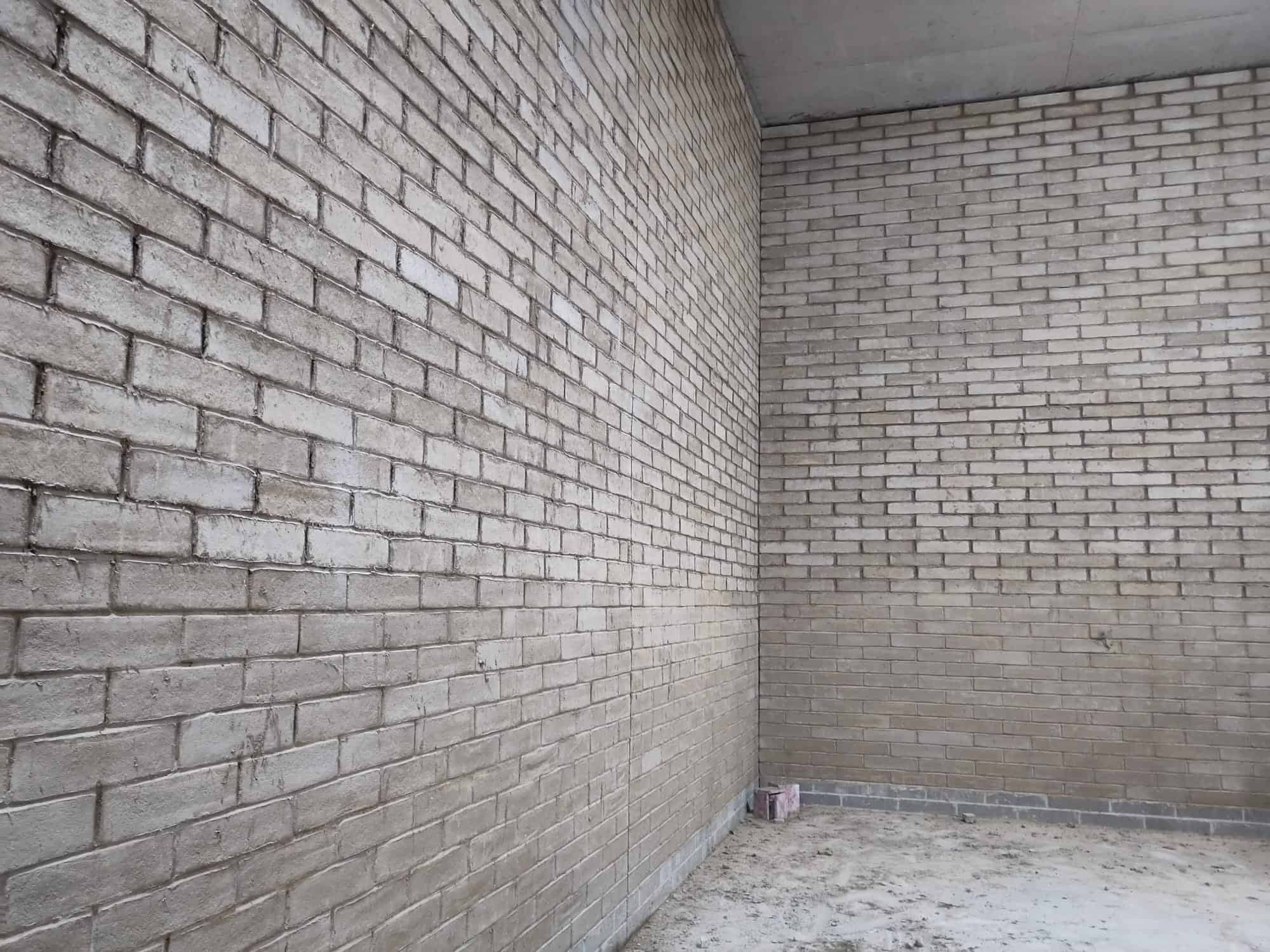
Problem addressed
Unfired clay in production has very low emissions. Two impacts are unavoidable in construction – extraction and transport, the third is drying instead of firing which is the biggest saving of the three.
In use clay can be structural but in sustainability terms its mass means it can be used to buffer heat in both hot and cold weather, a major saving. It also manages internal humidity meaning air quality, health and well being are improved without mechanical electrical costs throughout the buildings lifetime. Clay also sequesters VOCs, particularly formaldehyde, a major indoor pollutant.
Unfired clay is fully reusable/recyclable.
Case study
Developers gs8 produced The Arbour in 2022. It is a mixed housing development which used the spoil produced from the foundations to make Strocks for use in the party walls. Although the structure is a high performance Passivhaus design with structural timber throughout the blocks serve a number of functions in the building. From the developers perspective the savings in land fill tax was a major reason to use the process and a cost saving. The buildings have sound and fire attenuation through the use of the blocks and in an unfinished condition they provide a character and aesthetic which have added to the value of the finished products.
The unfinished blocks also improve the indoor air quality, very important for tightly sealed homes with HVAC systems and sequester VOCs, equally impactful in draft free homes.
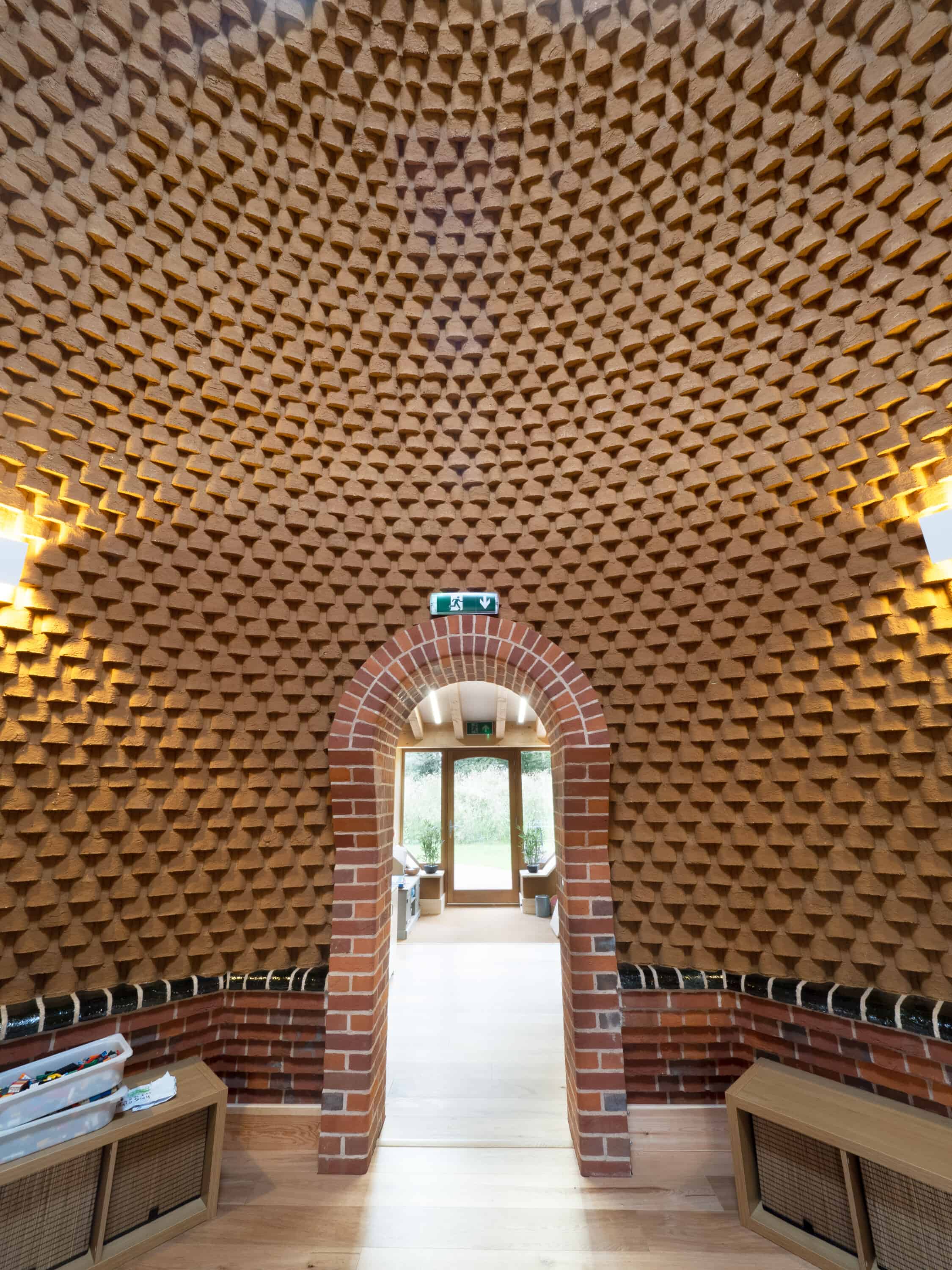
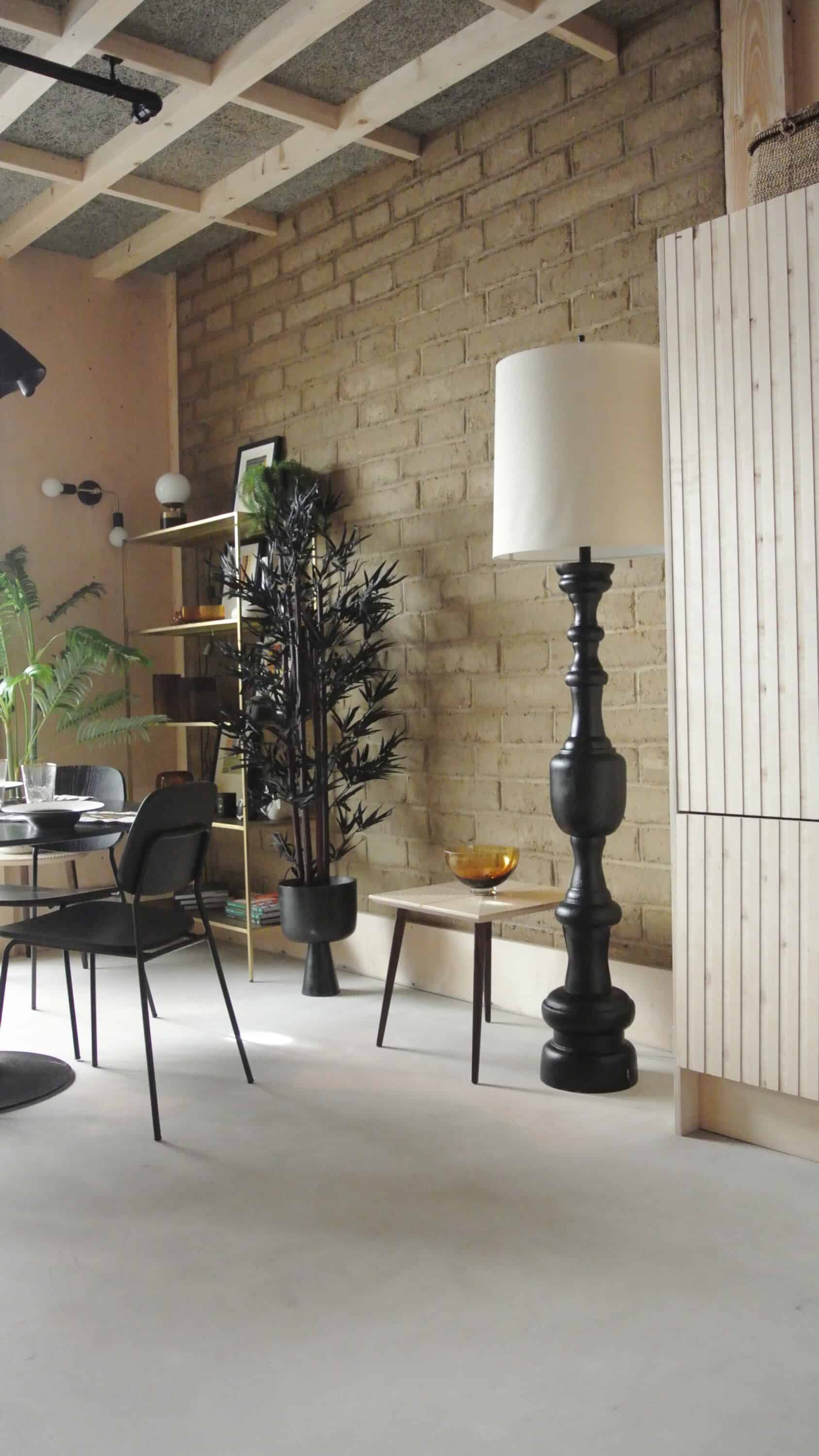
Facts and Figures
This page presents data, evidence, and solutions that are provided by our partners and members and should therefore not be attributed to UKGBC. While we showcase these solutions for inspiration, to build consensus, and create momentum for climate action, UKGBC does not offer commercial endorsement of individual solutions. If you would like to quote something from this page, or more information, please contact our Communications team at media@ukgbc.org.
Related
Database of sustainable building products
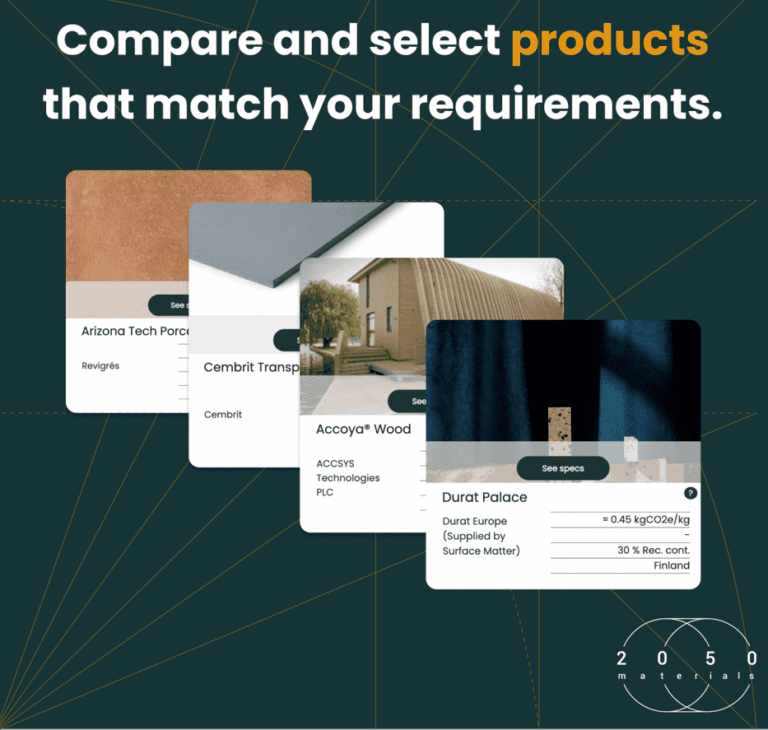
Zero cement concrete
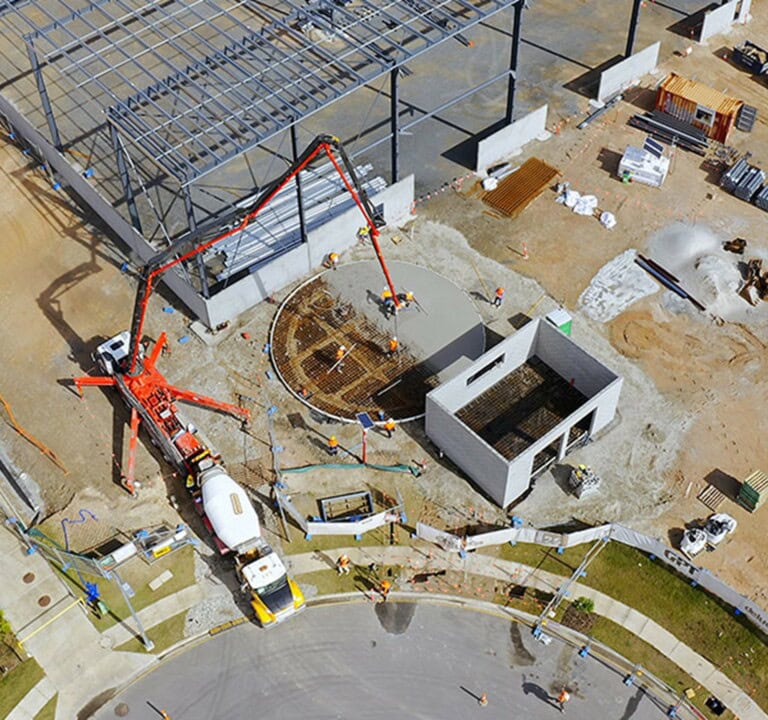
Product selection platform
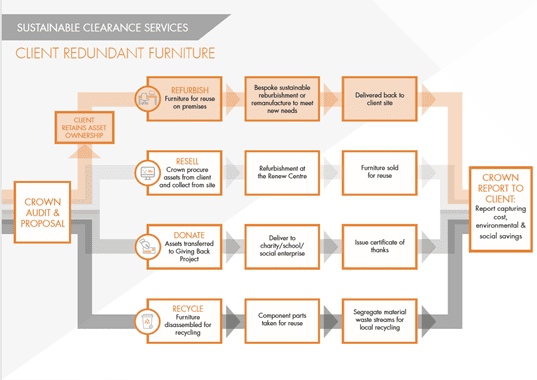
Bricks made from industrial waste
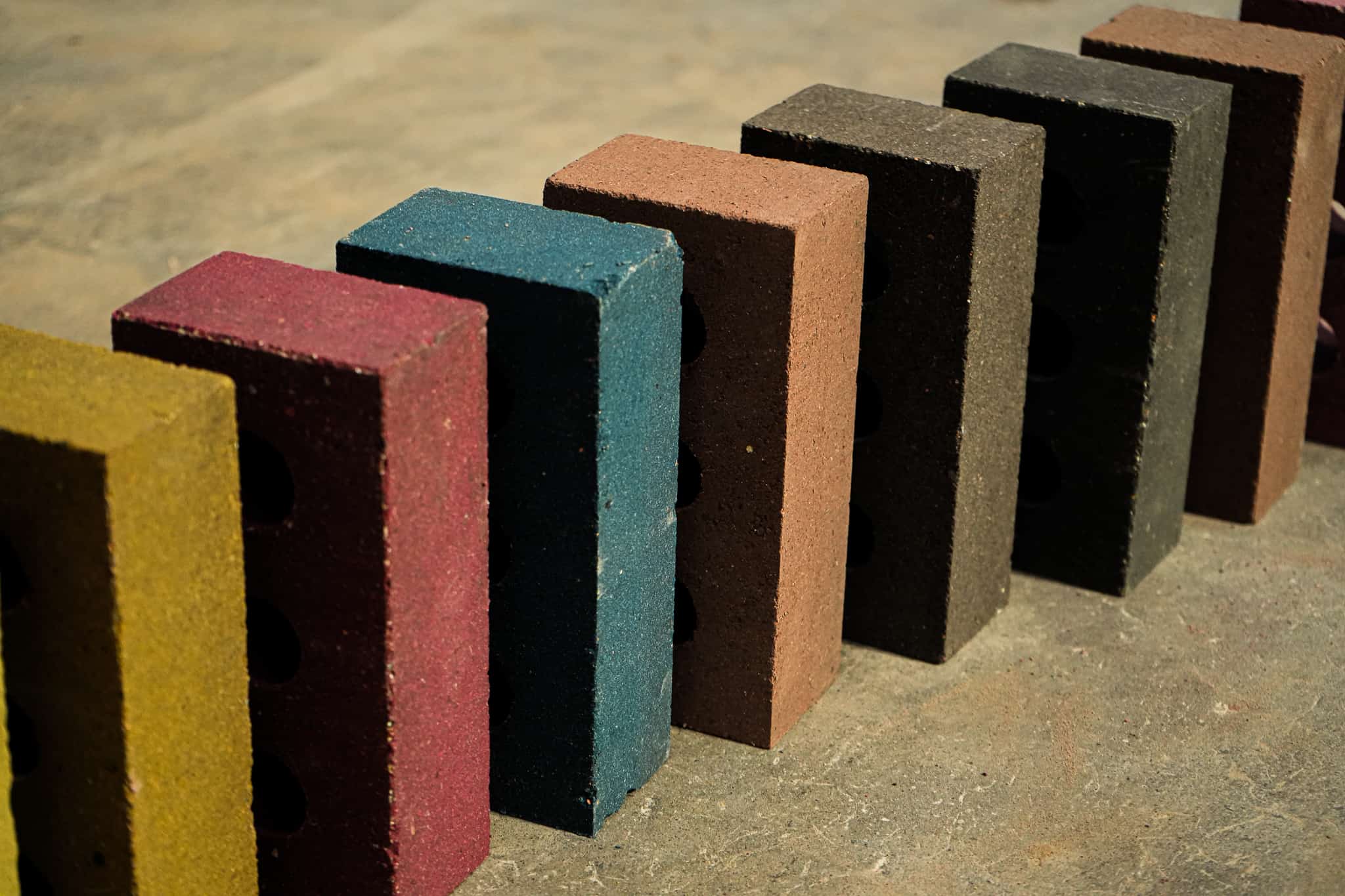