Robotic installation of underfloor insulation
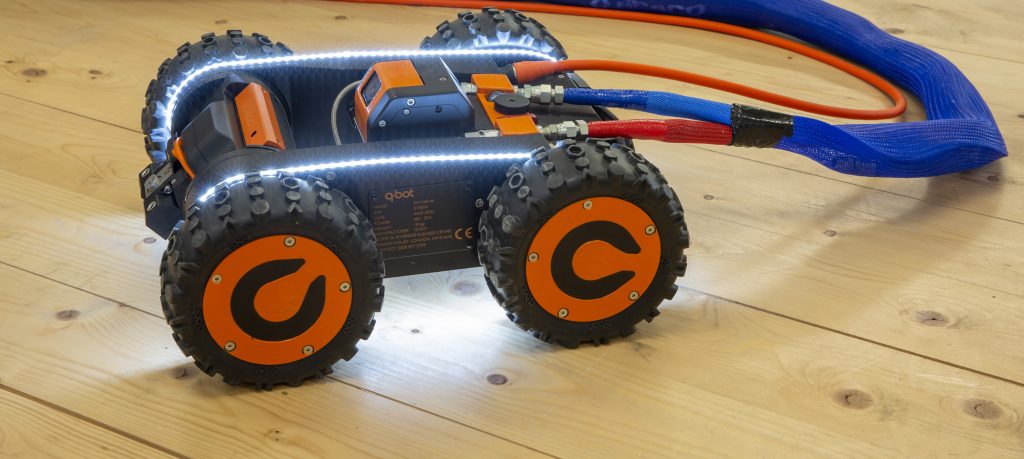
Problem Addressed
How to help enable the UK to meet its ambitious climate change and carbon reductions targets by addressing the problem of uninsulated suspended floors. The UK has some of the least efficient housing stock in Europe and energy use in homes accounts for approximately 14% of UK greenhouse gas emissions. An unprecedented effort will be needed to upgrade the UK’s 28 million homes to modern standards in order to meet the challenge of climate change.
Suspended floors can be a significant cause of heat loss in homes (up to 20%), potentially as much as through an uninsulated loft or cavity, or solid wall. The void beneath the floor is cold, as ventilation bricks are installed to avoid problems with damp, meaning draughts fed by cold air from outdoors can come up through the floor. There are about 8 million UK properties that would need to be retrofitted. Underfloor insulation is probably the next best step for energy efficiency and saving money on your bills, while reducing the UK’s carbon footprint.
Case Study
The case study noted above across 100 homes can be found here.
Q-Bot has also worked with more than 40 local authorities and housing associations across the country to upgrade their housing stock, such as Peabody, Clarion Housing, The Guinness Partnership, Torus, Castle Rock Edinvar, Nottingham City Homes and many others. As an example, Q-Bot installed underfloor insulation to 63 properties of Ealing Council with a variety of property types with suspended timber floors in London, starting in September 2019. Q-Bot achieved a 76% reduction in heat loss through the floor and an estimated 27% reduction in cold draughts. A pre-install survey checked the property for suitability, and during this the surveyor advised the tenant about the install process.
Installs were typically completed in one or two days, during which time the tenant was able to remain in the property, and experienced minimal disruption. A number of access hatches were made in the floor to allow the robot to access the void, at the end of the install the flooring was made good and the tenants signed off to agree they were satisfied with the work that had been carried out. The U value of the floor in all homes after installation of underfloor insulation complies with the Part L1B requirement for upgrading retained thermal elements in existing dwellings of <= 0.25 W/m 2 K. Expected savings per property are:
• Average Energy Saving: 1,940 KWhrs/yr
• Average SAP Improvement: 3.2 points.
• Average CO2 Saving: 400kgs/yr
• Lifetime Savings across all 63 properties: 1,070 tonnes of CO2
Case studies with other social housing providers can be found here, including Camden Council, Argyll Community HA, Hexagon HA and Castlehill HA.
Facts and Figures
This page presents data, evidence, and solutions that are provided by our partners and members and should therefore not be attributed to UKGBC. While we showcase these solutions for inspiration, to build consensus, and create momentum for climate action, UKGBC does not offer commercial endorsement of individual solutions. If you would like to quote something from this page, or more information, please contact our Communications team at media@ukgbc.org.
Related
Autonomous AI HVAC optimisation
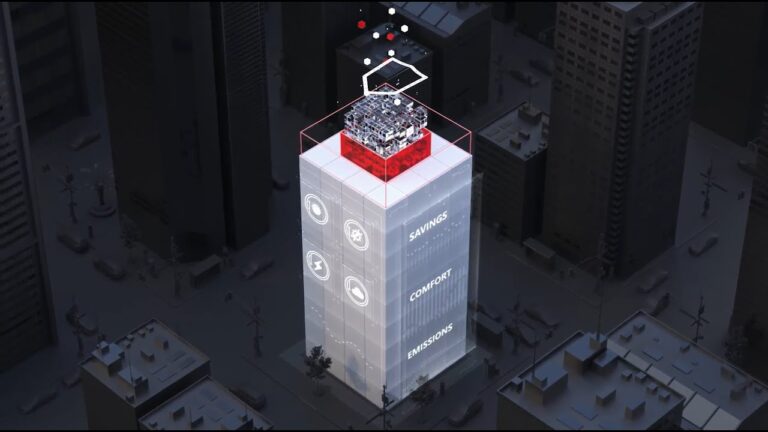
Assessment tool to help landlords design and implement retrofit programmes
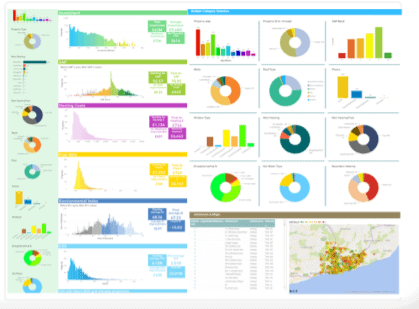
Insulation boards made from meadow grass
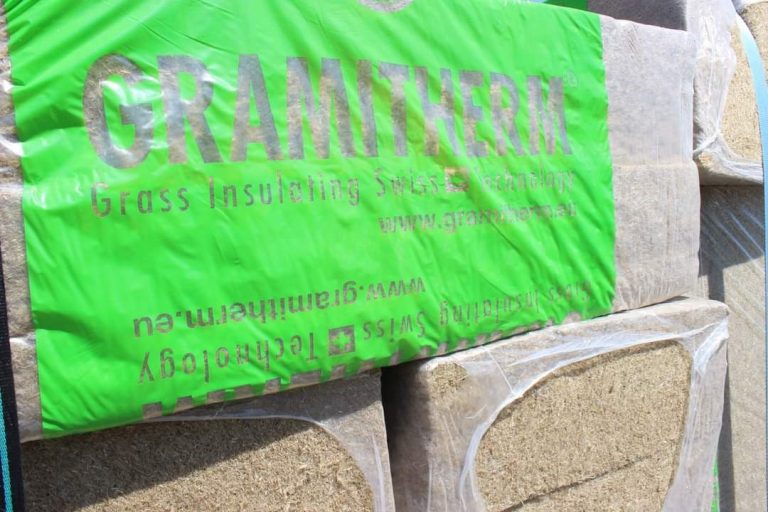
Insulating render / plaster
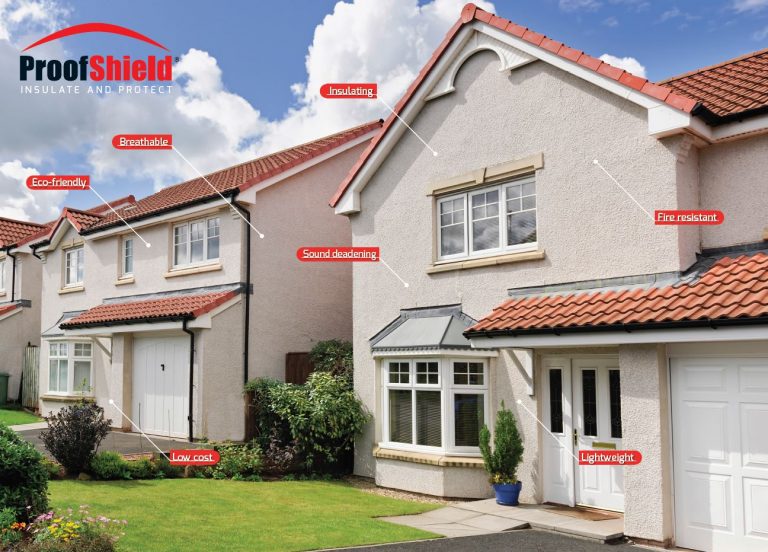