Steel reuse – Substation Screen

Key Sustainability Objectives/ Outcomes
On the reused steel purchased, 33.46T there has been a carbon saving of approximately 66T CO2 but further savings of 22T CO2 approximately have been lost as new material was selected over reused.
The further savings were not achieved despite the steel being independently tested and weld inspected in accordance with the SCI protocol. A few pre-existing holes and the random lengths of the steel meant the fabricator rejected them over concerns of extra work or potential dimensional clashes and yield. The cost of the reused steel was 30% cheaper than new which would have created further cost and carbon savings for the project.
Notable Approaches And Solutions
At the initiation of the project the client requested reused materials. The architect approached CST with a range of steel sizes which could be utilised in the project. CST then provided an inventory of the steel available that was both within their required ranges and was also going to offer advantageous cost benefits.
By having an “open” specification at the start, the design was able to accommodate the information about material options offering maximum CO2 benefits. These materials were then incorporated into 3 different preliminary designs.
By involving material suppliers early, it meant the supplier was aware of the client requirements and could find and hold material useful to the project. This is fundamental in the reused market as it is still in its infancy and growing. It is not and may never be a mirror of the new material marketplace as reused material cannot be “made on demand”.
However, in this case, pre-sourcing the materials did not result in securing the lowest carbon outcome. As the design kept changing and the structure was value engineered purely on a weight and cost approach some of the steel needed had to be sourced new, reducing the carbon savings which would have occurred through reused steel.
It has also cost CST as the prices were honoured for over a year during which time steel prices had almost doubled. This is not viable normally but causes questions about feasibility of projects that take so long to come to fruition but rely on pre sourced material.
Lessons Learnt
- If material is to be pre-sourced, then it is critical that the design is finalised, or the design parameters are fixed otherwise the material may simply become irrelevant. Steel design is problematic as architects design, steel work design and connection design can all be carried out by different parties. If architects require reuse, then it is important that the reuse parameters are fixed early in the project otherwise the reuse opportunities can be designed out by the engineers or connection designs as they seek to “improve” or rationalize the design.
- If the reused material is to be pre-sourced, then an overall manager of the project through the whole supply chain process is crucial. Otherwise the message and mission can easily become lost or each part of the chain has to be reassured about reuse etc. as they are introduced to it.
- If material is not going to be pre-sourced and the design cannot be adapted to materials at the time of fabrication, the reused content cannot be fixed or even estimated.
- If reuse is not specified, then “buyer inertia” or “business as usual” is likely to prevent reuse occurring.
- Reused material may require pre-use surveys to assess suitability and cost effectiveness. If the drawings are with the fabricator and the material with a vendor then this assessment is less simple and will result in aversion to use the material or could result in material being un–usable. As a vendor we will be doing material surveys against drawings wherever possible.


Related members
Related
Refurbishment and redevelopment of the Old US Embassy
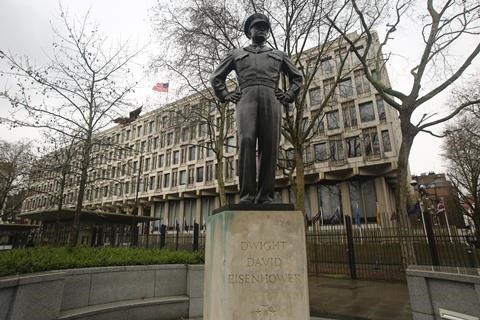
1 Triton Square
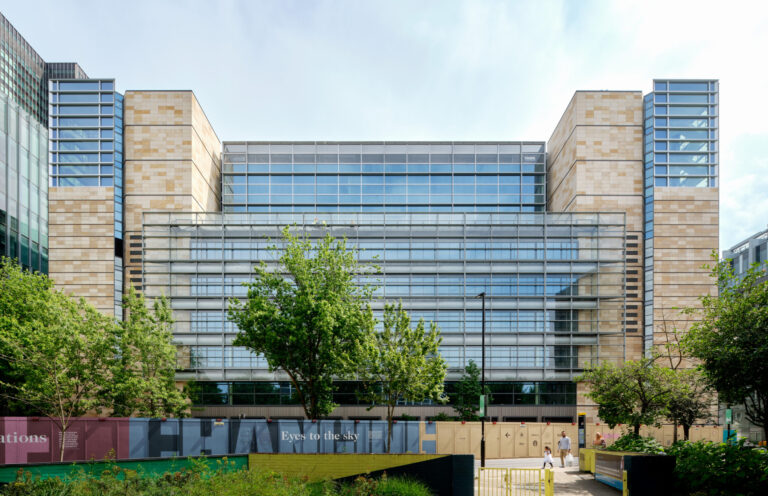
Reused and repurposed steel tubes and sections
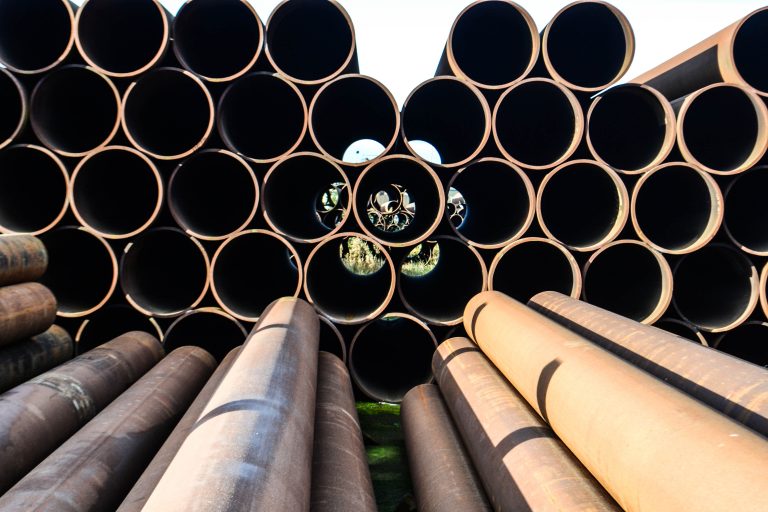
3D printed concrete beams designed to use less material
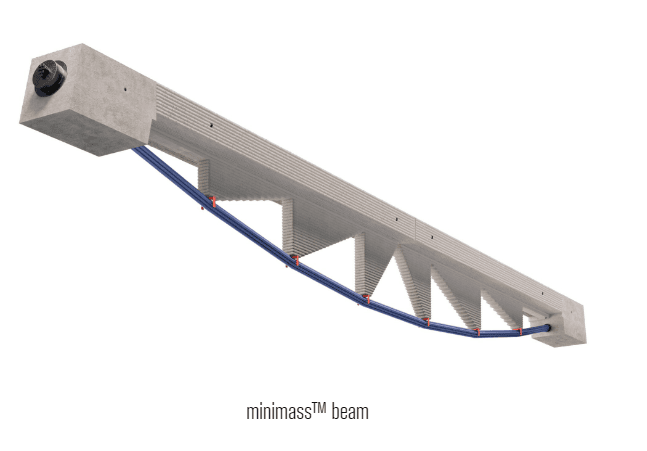