Closed-loop recycling scheme for waterproofing

Problem Addressed
One of the primary forms of below-ground structural waterproofing are cavity drain membranes, manufactured from High Density Polyethylene. However, every year the waterproofing industry sends thousands of tonnes of membrane waste to landfill. Although the waste is too small to reuse in the waterproofing industry, it is made from virgin High Density Poly Ethylene (HDPE) that is perfect for recycling.
Case Study
Newton’s relationship with Mace began in 2015, when Newton won the right to supply one of London’s largest below-ground developments. However, it was in 2017, when the recycling service was introduced, that the relationship became a sustainability collaboration. For example:
- Mace’s Sustainability Operations Director featured in Newton’s launch video.
- Newton began working with Mace’s Sustainability Team to calculate the savings achieved by the service, which were featured in Mace’s internal company newsletter.
- Newton assisted Mace’s 2018 initiative to reduce single-use plastics, also becoming a ‘suggested supplier’ in a new action plan for reducing waste. The business-wide plan was implemented at the start of 2019, vastly increasing company exposure.
- In January 2019 Newton appeared as a guest speaker at a private sustainability event hosted by Mace for 250 of construction and sustainability contacts.
- Newton have continued to deliver recycling and sustainability data on an individual project basis – For example at the construction of the two-storey basement beneath the London School of Economics’ new Marshall Building in London. 115kg of membrane waste was successfully collected and recycled by our specialist contractor from this project alone, and Newton issued Mace’s Sustainability Team with the data and a certificate to recognise the achievement. Read the full case study here.
This level of exposure at the top tier of UK construction would not have happened without the recycling service, and Newton are continuing their sustainability collaboration with Mace on further projects.
This page presents data, evidence, and solutions that are provided by our partners and members and should therefore not be attributed to UKGBC. While we showcase these solutions for inspiration, to build consensus, and create momentum for climate action, UKGBC does not offer commercial endorsement of individual solutions. If you would like to quote something from this page, or more information, please contact our Communications team at media@ukgbc.org.
Related
Collecting and donating surplus furniture, equipment and materials
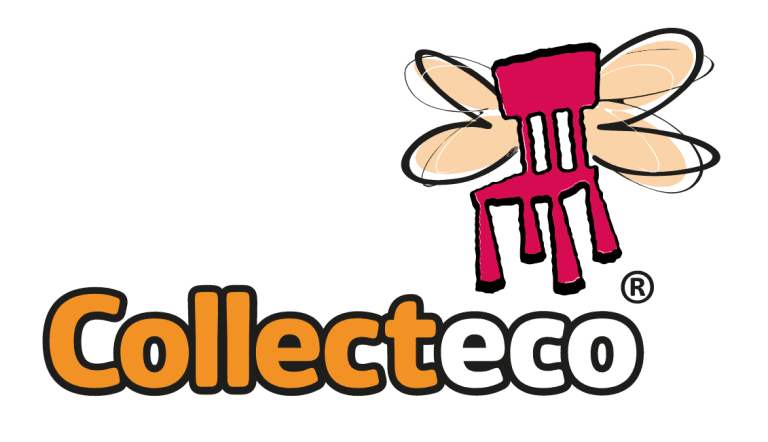
Digital reuse platform
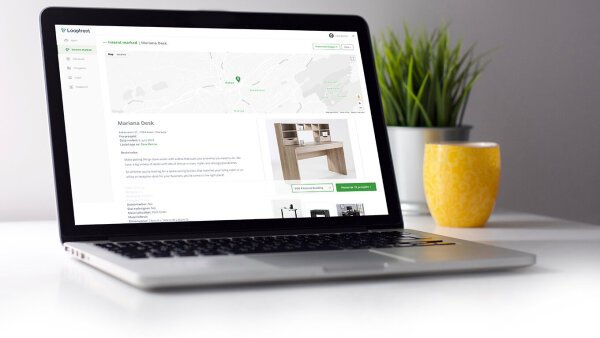
Spaces for the sale, donation and recycling of items
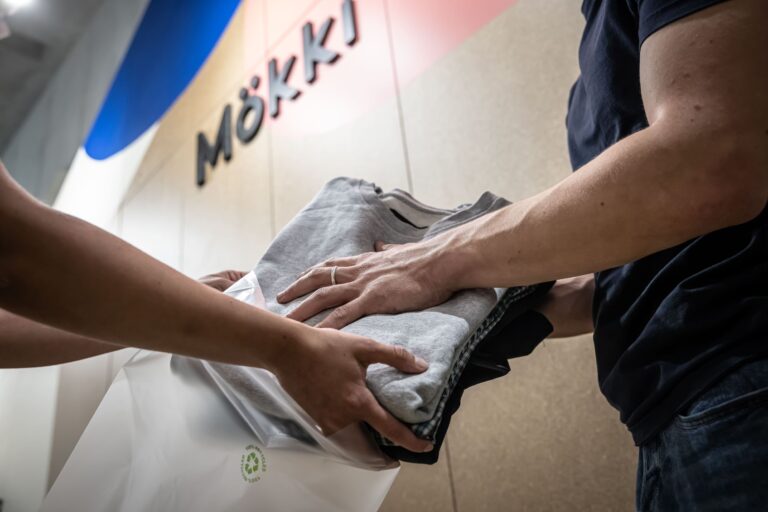
Materials Passports Platforms
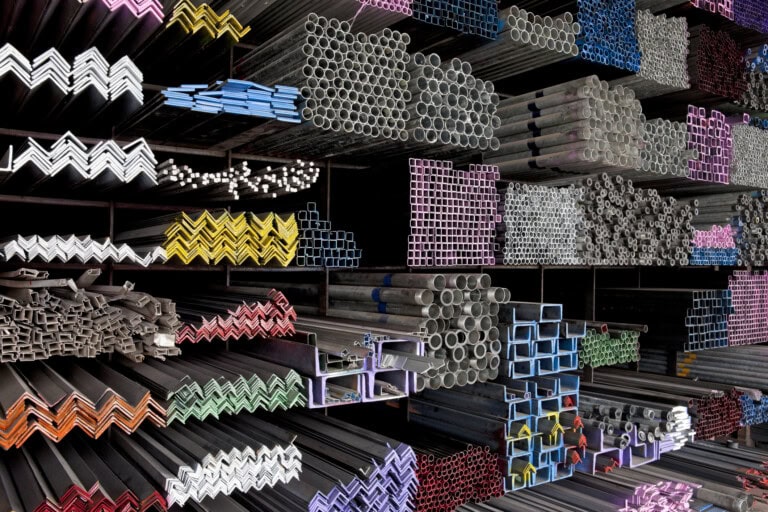