Comfort Frame Limited
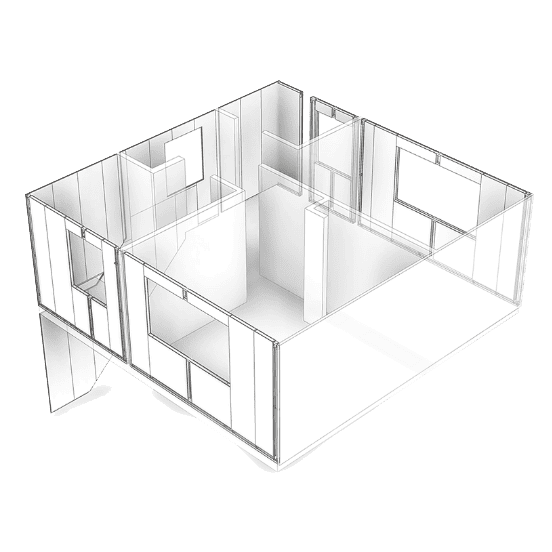
Problem addressed
To ensure buildings are energy efficient and compliant, thermal upgrades are necessary. Internal wall insulation (IWI) is one method to improve a building’s energy efficiency, however, many IWI solutions can struggle with providing an effective u-value while improving draught proofing and reducing heat & moisture transients.
Overview of start-up
Comfort Frame design, manufacture, and supply a unique and innovative IWI product for reducing a building’s energy consumption. Their walling system is highly resistant to mould/damp and does not encourage the growth of bacteria or fungi. Post installation, this ensures that their systems can help create a healthier environment for occupants. Since the wall system is both Design for Manufacture and Assembly (DfMa) and utilises offsite MMC, their systems are both bespoke to the property they will be installed in while minimising waste created during both the manufacturing and installation process.
What makes the start-up innovative?
Comfort Frame’s unique innovation differs from traditional IWI systems by being isolated from external walls. A self-adhesive vapour permeable air barrier allows walls to ‘breath’, which mitigates the risk of damp and mould. The thermally laminated panels and unique compression system provide unrivalled thermal upgrades, having the combined effect of increasing heat within properties whilst also reducing energy consumption.
In terms of the customer journey, it is also important to note that Comfort Frame’s system minimises disruption due to the fast nature of its installation. Typical elevation can be installed in one day with tenants remaining in situ.
How the start-up has been designed to scale-up quickly
Comfort Frame is at the forefront of MMC. Their DfMa process starts with a point cloud survey of solid walled/hard to treat properties. After this, they then manufacture their IWI systems bespoke to the measurements, maximising quality while minimising waste. They are committed to accelerating retrofit and their in-house manufacturing has the capacity to produce around 20 projects per calendar month. The complete process from survey to manufacture is complete within a matter of weeks.
The IWI system arrives on site in a kit of parts that are designed with ease of installation and maximum efficiency in mind. Comfort Frame have recently completed a project which had 32m2 of wall which they installed in only 5 days – including decorating. Based on project forecasts, they have the capability and capacity to deliver in excess of 200 projects per year.